In order for these warehouse processes to run smoothly every day, it's smart to take safety, quality and efficiency actions along every step of the way. Curious what that looks like? Quickly read along!
Take these 6 fundamental actions for warehouse optimization
Alright, so now you know which processes your warehouse management should consist of. But how can we make these run as smoothly as possible?
By implementing the following key strategies, you will streamline processes, improve inventory management. Here is how to run an efficient warehouse:
- Maximizing and optimizing space: Make the most of your warehouse by utilizing every inch of available space. This means investing in proper storage systems, so try to refrain from using broad and low shelving and use vertical storage solutions instead.
- Track Key Performance Indicators (KPIs): Identify and monitor relevant KPIs, such as order fulfillment rate, inventory turnover, and picking accuracy. Regularly analyzing these metrics will allow you to identify areas for improvement and make data-driven decisions.
- Use labeling systems: Implement a comprehensive labeling system - including text and colors - for inventory, storage locations, and shipments. Clearly labeled items and designated storage areas reduce picking errors and save valuable time during order fulfillment.
- Organize according to your customers: Consider the needs and preferences of your customers when designing the layout of your warehouse. Group together items that are frequently purchased together to facilitate faster picking and packing. You'll reduce the time required for order fulfillment if you place the most popular items in easily accessible locations for your employees.
- Ensure quick preparation: By implementing efficient picking and packing strategies such as wave or batch picking, you minimize errors, and reduce the time spent on each order. Also consider opting for using barcode scanners and RFID to enhance speed and accuracy.
- Outsource to 3PL: No need for a one-man show! Referring to Third-Party Logistics, a 3PL provider offers a range of services related to inventory storage, distribution, and order fulfillment. By leveraging an expert, you can use their infrastructure and technology to run your warehouse more efficiently.
By implementing these steps from different disciplines, your warehouse is ready to take on various challenges. However, not all successes come from preps or labels…
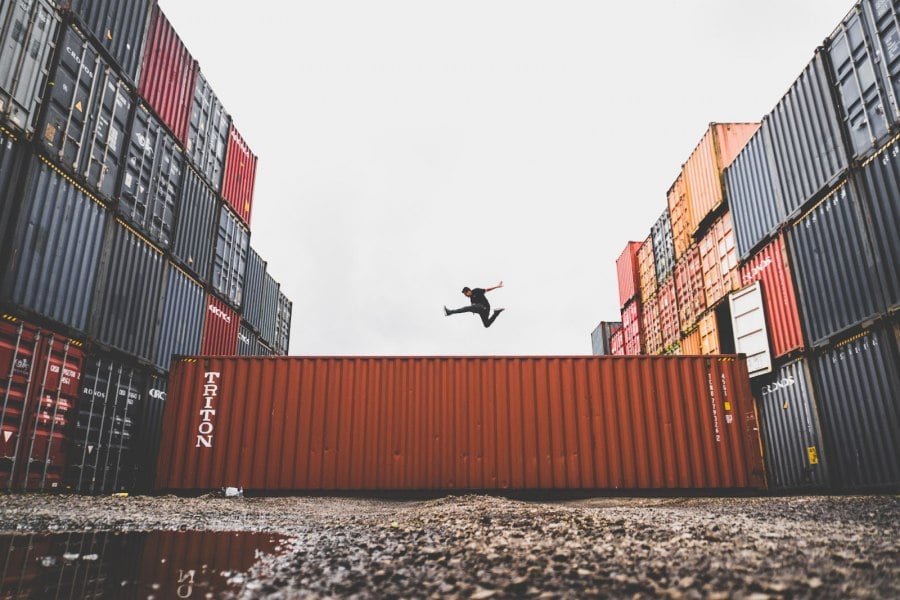
Go the extra mile: bringing work satisfaction to the warehouse
So you find your business is starting to kick off as orders are coming in regularly, keeping your team busy. But how do you make sure the efficiency of your warehouse will last for long? By bringing fun into the game of course!
One of the keys to business success is employee satisfaction. First and foremost, it is important that your team knows the ins and outs of the warehouse operations and that they are familiar with the warehouse management software. After that, you can keep the spirits up on a daily basis by for example:
- Creating colored workstations: Designate specific colors for different areas or types of workstations within the warehouse. For example, you could assign the color yellow to receiving and inspection stations, blue to packing and shipping stations, orange to quality control areas, and so on. This way, you lift up the mood by using happy colors and improve the chances that the warehouse will always be organized correctly.
- Personalizing work gear: Provide your team members with custom patches or badges that they can attach to their work gear, such as safety jackets. These patches can include their names, nicknames, or even symbols that represent their interests or hobbies! By doing this, you create a sense of belonging and individuality among your team members, making them feel valued and appreciated.
- Creating a suggestion box: Encourage your employees to (anonymously) share their ideas and suggestions for improving warehouse operations, either in a physical suggestion box or digital platform. Regularly review the submissions and acknowledge and reward employees whose suggestions are implemented. This not only promotes employee engagement but also demonstrates that their opinions are valued, giving them more motivation and excitement to show up to work the next day.
- Celebrating milestones and achievements: Invest in the art of celebration! Recognize both small and big milestones, such as reaching business targets or achieving individual sales goals. Consider organizing parties or asking people to bring their favorite treats or snacks after successes. Celebrations create a positive and motivating work environment, and they show your appreciation for your team's hard work!
Another important way to create employee satisfaction is by taking out the bad stuff. In other words: solving the most common warehouse frustrations, like accidentally planning broken equipment. Luckily, there is an easy solution: implementing a Warehouse Management System!
Go digital: invest in a Warehouse Management System
Managing a warehouse is an all-encompassing task, so implementing a warehouse management system (WMS) will be able to bring numerous benefits. A WMS can automate and streamline inventory management, which we are all too familiar with.
So, we created software that simplifies your warehouse management. With Rentman, you can:
- Create equipment databases and digitize your warehouse, which enables you to store detailed information for each item, based on its serial number.
- Use digital packing lists to ensure the correct gear leaves the warehouse and reaches the right hands.
- Import and manage inspection results, allowing you to track past inspections and repairs for each gear item, right down to the serial number level.
- Access the equipment timeline and perform quick searches to know what you have in stock at any given moment.
- Generate reports to support better purchasing decisions, reducing the need for frequent subrenting of equipment.
With all these functionalities, your crew will have full autonomy and reduces the number of mistakes they make. This leaves you with more time to work on your business and make better purchasing decisions!