RFID: warehouse management as a solution to human errors
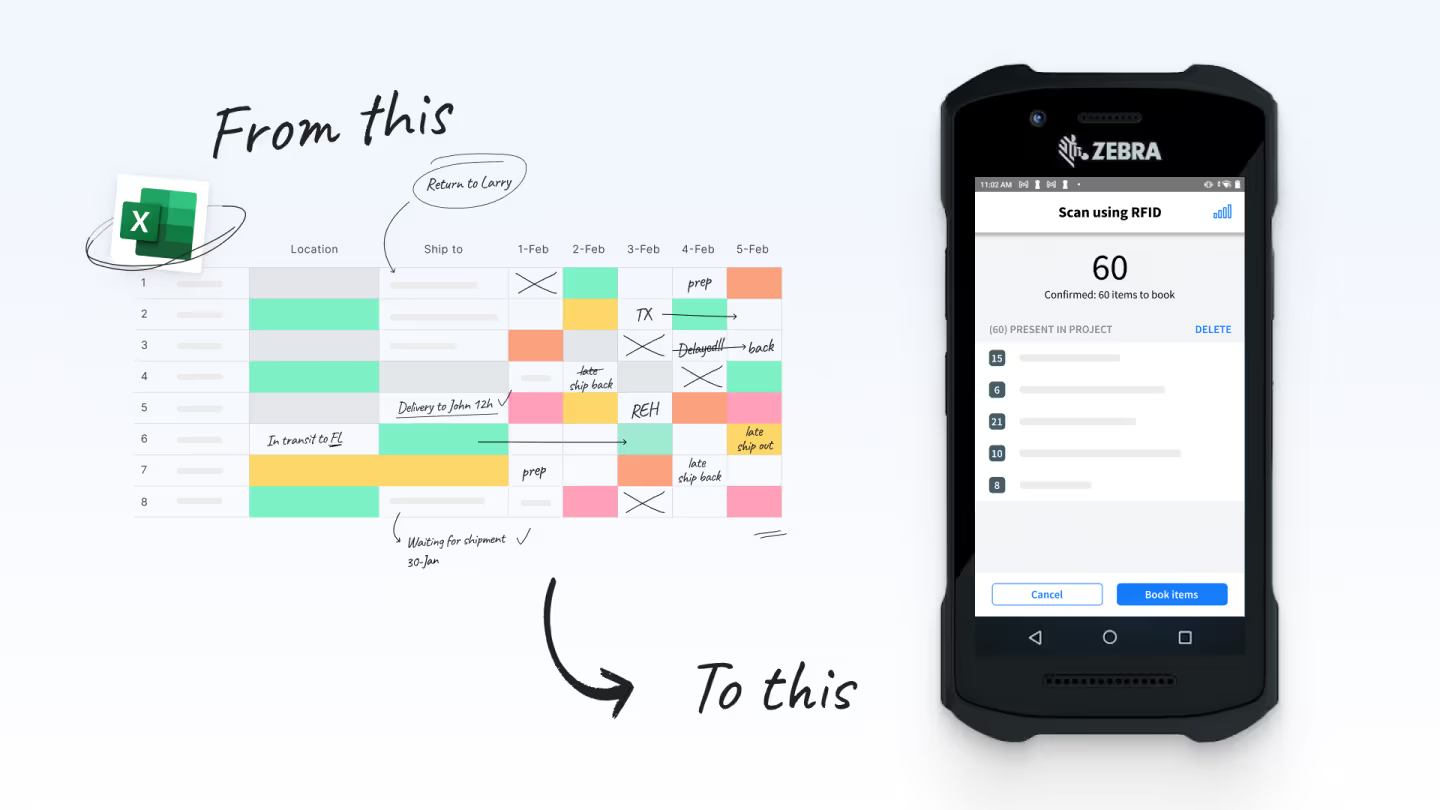
The AV industry has entered a new phase in the aftermath of the COVID era. While the impacts of COVID have receded from our daily lives and work routines, it's clear to AV professionals that since 2021, there has been a notable upswing in the workload. Fortunately, leveraging RFID for warehouse management might offer release.
Do you feel like your workload has doubled since 2021? Then you're probably right. Compared to 2021, we've seen a surge of 79.8% in completed projects in the past year. And (spoiler alert!) even though 2023 is only halfway through, the number of completed projects is already on par with last year.
What’s more, the nature of projects has changed. Presumably, most owners did not double the equipment in their warehouses to keep up with the rising demand, which means they need to make do with less equipment than they’d like. Our data confirms this. Equipment planned for projects dropped by 17.8%.
Instead, we're outsourcing more; compared to the first two quarters of last year, there's been an 11% rise in crew projects. This results in more complex planning, leading to logistical challenges for the sector.
A sudden increase of staff may be detrimental
More hands on deck doesn’t always translate to smooth sailing. In fact, AV professionals are reporting an increase in incompletely packed productions, due to an influx of new staff.
How come? While experienced warehouse workers can mentally prepare and pack for productions - they can perfectly anticipate and know exactly which items need to be set aside to be used again later in the day - newer employees often lack these skills due to the absence of proper onboarding and efficient workforce management.
This leads to inaccurately packed projects, stock issues, and unexpected surprises.
2 simple steps to avoid inaccuracy
- Review equipment configurations. Are they complete, up-to-date, or frequently adjusted within a project? Accurate equipment configurations require fewer clicks, giving warehouse staff clearer and more comprehensive instructions.
- Never underestimate the power of a physical label in a flight case specifying its contents. It's not just an effective way to guide new staff or freelancers on-site but it’s also useful for dry hire customers.
Pro-tip: Remember that loading and unloading often takes place in relatively dim lighting. Therefore, maintain as high a contrast as possible in any visuals or images.
Making AV warehouses 'idiot-proof' will result in fewer defects and streamline project planning and execution. But if the goal is to truly gain more control, then more is needed - such as an RFID inventory system.
Increase traceability with RFID warehouse management
With RFID, items can be scanned without physically searching for a QR or barcode, meaning you can scan without ever opening a flight case. A massive time saver in the warehouse. How does this work? We use RFID tags for inventory to become traceable. Each piece of equipment will be tagged and can then be scanned from a (short) distance.
As a result, with RFID, we can scan a meatrack of fixtures in just three seconds. With QR codes, it takes thirty seconds.
The ease of using RFID in the warehouse? It allows equipment to be scanned on-site. If the list isn't complete, the search for missing items can start immediately. If items are truly lost, this can be processed faster, allowing more time to address any resultant equipment shortages. Test cases show that using RFID reduces the time spent locating lost items by over half.
Do you have a grip on the traceability of your equipment movements? RFID is rapidly gaining traction in the industry, with more companies integrating it into their daily processes. Evolve with the industry; streamline and expedite your warehouse activities and enhance accuracy with RFID.
FAQ
Frequently asked questions
No items found.
Previous blog posts
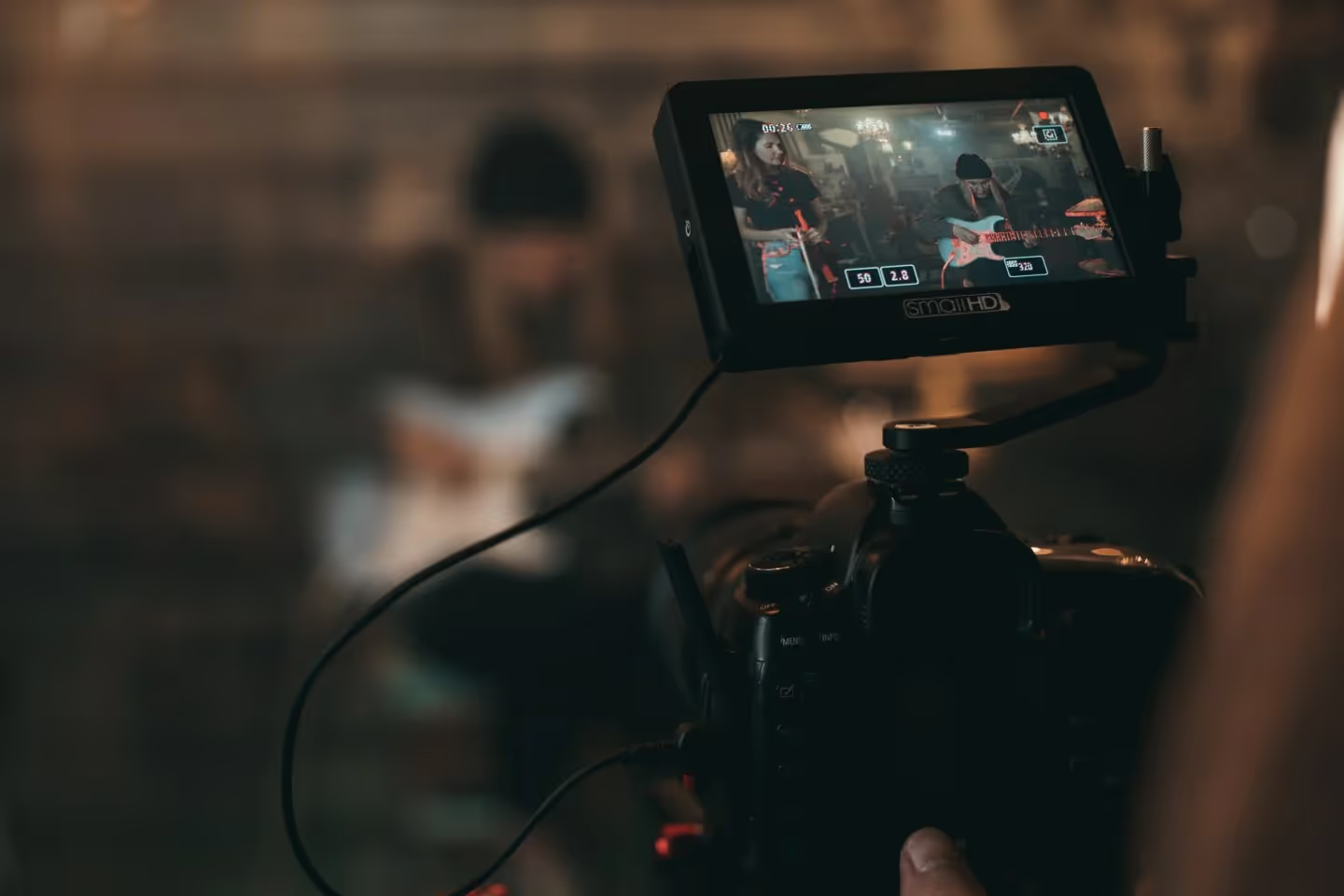
What you need to know about equipment rental insurance: cost, coverage, and requirements compared
What you need to know about equipment rental insurance: cost, coverage, and requirements compared
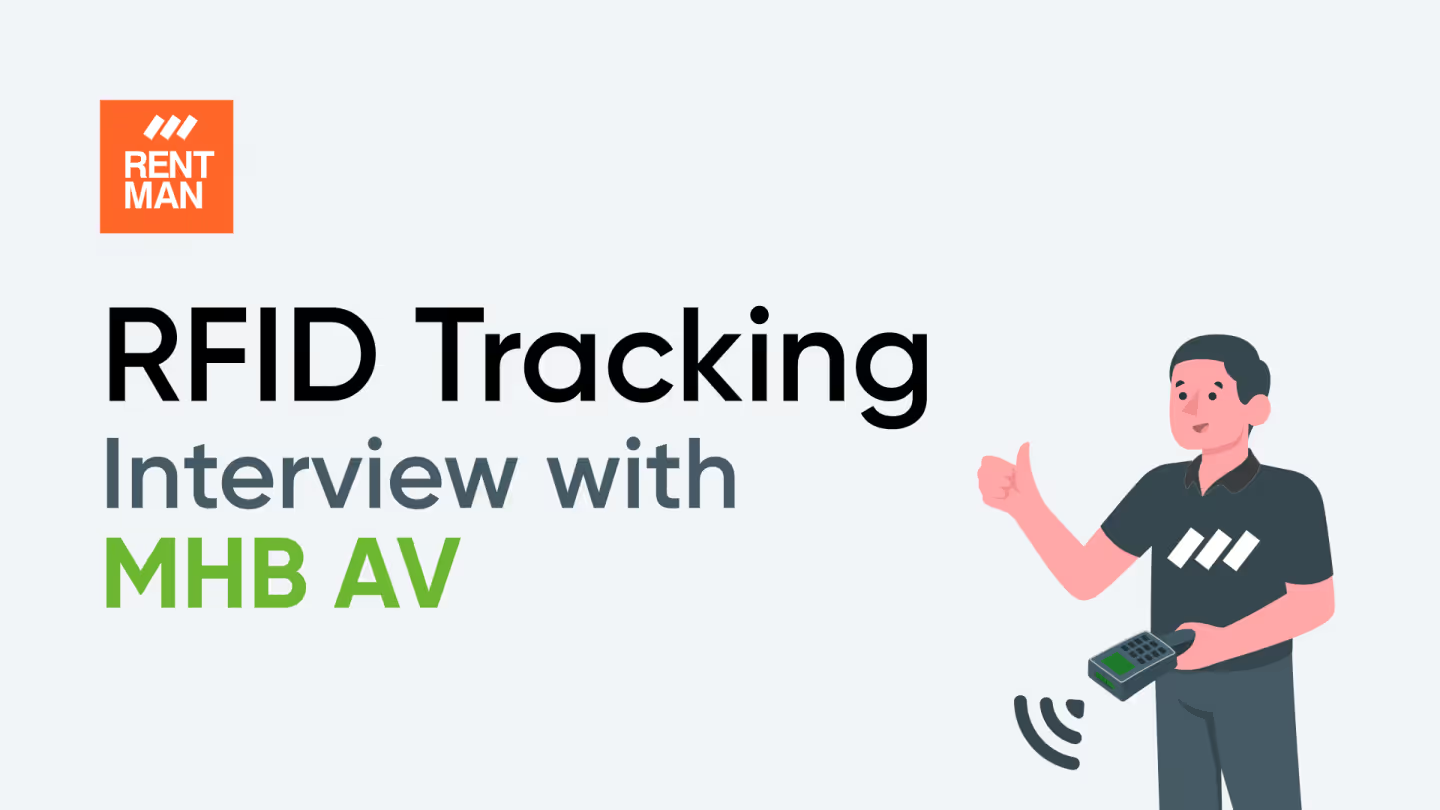