How to optimize your inventory using Rentman
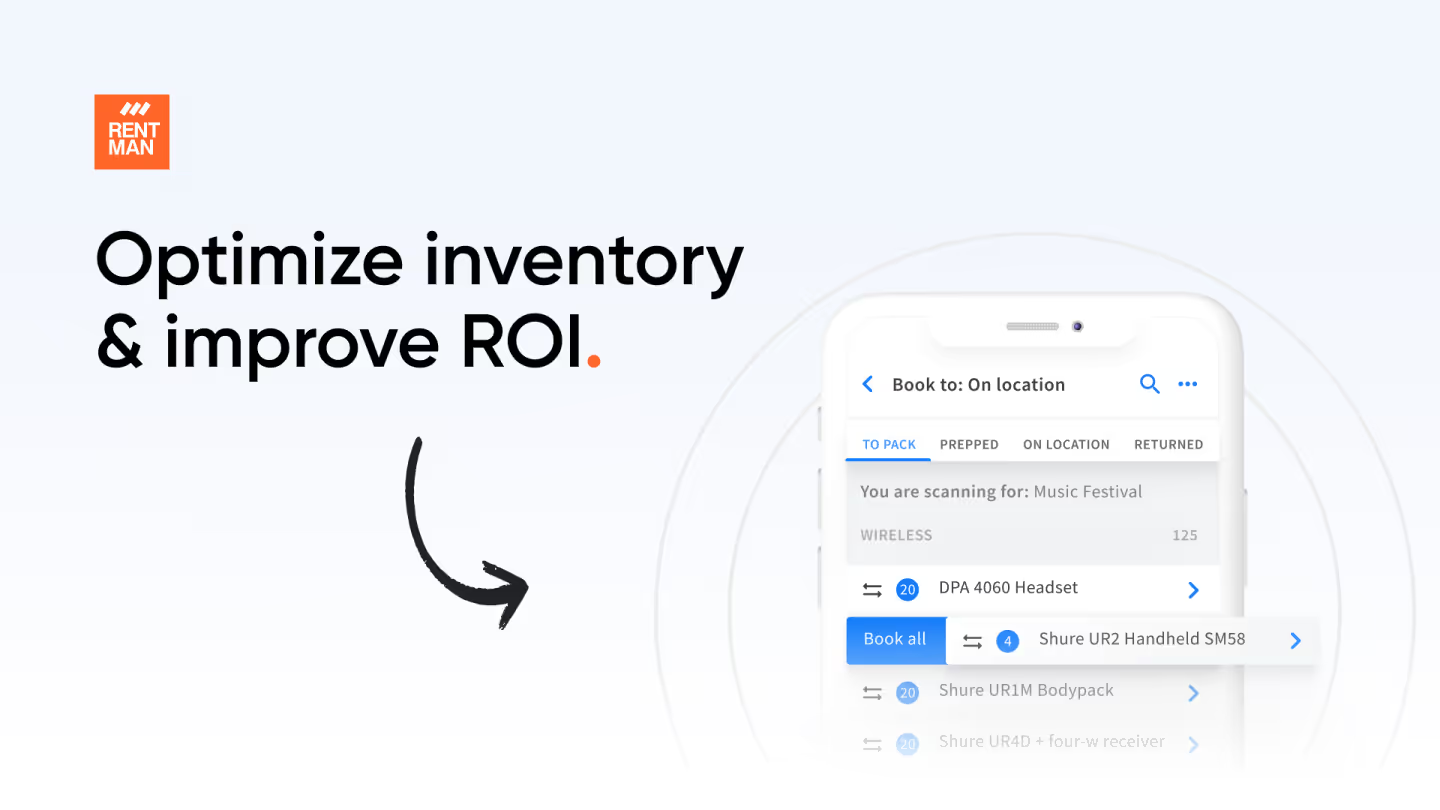
Your inventory is a crucial part of your business. To keep costs low, avoid waste, and keep your customers happy, inventory optimization is a must.
But how to best keep track of items that come and go continuously?
In this blog, we’ll give you strategies to optimize your inventory to ensure you stop losing items and keep your company's ROI high. And we’ll give some examples of how to tackle those challenges using Rentman
Here’s what we’ll cover:
1. How to organize your inventory
2. How to know when to reorder items
3. How to track items when they leave your warehouse
Organize your inventory to manage it with confidence
Whether you’ve just launched your rental business or have been in operation for a few years, the first step to optimizing your inventory is to organize it. Why? Inventory control allows you to know exactly what you have, how much you have, and the location of each item.
Record all of your equipment
You need to know what’s in your warehouses. Without a clear overview, you will underuse some pieces of equipment, double-book others, and be more prone to making mistakes.
So start by recording all the gear that’s in your inventory. But don’t do that manually. Save time and use an equipment management solution like Rentman. To upload new equipment, simply import your existing data from Excel or another software solution.
Bulk record certain items
Uploading individual items is easy. But what if you have hundreds of identical small items such as partywear or cutlery? You probably don’t feel the need to serialize and track every individual item. The solution is to bulk record items.
Bulk items are products you don’t need to specify individually as you check them out. Helping you to handle them faster. This is perfect for accessories and relatively low-cost items that you pick from your shelves at random.
Within Rentman, easily record these items entering the name and the quantity for that item. Saving you a lot of time when recording and optimizing your inventory and streamlining pickups and returns.
Stop losing items by adding their location
If you have multiple warehouses across different locations, you need to know which items are located where. So you need an inventory control system. Otherwise, gathering the right equipment for each event will be a nightmare.
Rentman simplifies this process. Set up multiple storage locations, name them as you prefer, and then allocate equipment accordingly. Whether it's bulk equipment or individual items with unique serial numbers, Rentman lets you assign and keep track of everything across different locations. Guaranteeing a smooth workflow and making sure you're always prepared for any event.
Add custom notes when needed
Managing notes about your stock items, as well as tracking repairs, serial numbers, purchase details, warehouse locations, and more, can be a struggle. Sometimes, you could use a place to store and share all of that. That’s why Rentman enables you to add detailed notes about a piece of equipment via custom fields. Making it easier to keep track of every detail such as an item’s warranty, maintenance history, or use instructions.
Implement notifications for reorder moments
Some items, such as batteries, you always need to have on hand. If you run out, chaos follows. Someone will be forced to run out and buy dozens of tiny packages, which cost more than ordering in bulk.
To avoid this situation, you need to pay attention to the stock levels of such items. But checking those numbers daily can be hard to remember. With this in mind, Rentman allows you to establish reorder points for items, triggering automatic notifications when quantities dip below specified levels. Ensuring you never run out of important consumable items.
Track items when they leave your warehouse
Armed with a clear overview of your gear, it’s time to ensure you stop losing equipment at events. As this ensures your company’s ROI stays high.
The best way to do this is to implement an equipment-tracking solution which gives you more control and a clear overview of the movements of your gear. However, there's more you can do for effective inventory optimization and keep tabs on your gear.
Implement RFID technology to keep tabs on your gear
Items shouldn’t disappear when they leave your warehouse. You need to be kept up to date on their movements and uses.
To do this, use RFID tags to track equipment in real-time and prevent unauthorized access. These tags come in different shapes and sizes and can easily be attached to objects so you can track them.
The best part is that you don’t have to be in an item’s direct line of sight to scan it. Use a handheld RFID reader to scan items 20cm to 10+ meters away.
An inventory control solution such as RFID enables you to always know where your gear is and facilitates hassle-free returns. Also, if you lose an item, simply check where it was last scanned to know exactly where it was last seen. Boosting your chances of finding lost items
Bundle frequently used items together for rental
Certain items will probably always be rented out together. For example, a camera kit will include a camera body, various lenses, and accessories. However, manually assembling such kits is time-consuming and makes you more prone to error. From packaging to opening up the case and scanning each individual piece of gear, the last thing you want to do is forget to pack an essential item.
For this reason, Rentman gives you the option to create containers and cluster items commonly used together in your inventory. For instance, when a client requests the camera kit, you can quickly select the combined items, instantly booking the complete set. Thus simplifying the booking process and ensuring all essential components are included.
And once you’ve set up containers, you can simply scan the QR code or RFID tag of your transport case to see what's inside. No need to open sealed cases and manually check their contents. Saving you time if a container holds tons of adapters, small items, and accessories.
See items incoming and outgoing within 12–48 hours
Some of your more popular pieces of equipment may have quick turnaround times. To keep your warehouse operations running smoothly and your inventory moving, implement an overview of items that have a turnaround time of less than 48 hours.
Within Rentman, use our cross-docking view to visualize items returning and leaving your warehouse in the next 12, 24, or 48 hours. Such a proactive approach ensures your equipment keeps moving at a steady flow and minimizes inventory disruptions.
Inventory optimization helps keep things organized
Optimizing your inventory is more than just a tactical move - it's a strategic investment in the growth and success of your business. Why? Because a streamlined inventory fuels operational efficiency and customer satisfaction.
And there are various ways you can go about optimizing your inventory. From creating a better overview of what’s on your warehouse shelves to tracking equipment when it leaves the building, pick the strategies that address your current challenges.
If you want to experience how equipment rental software can help you grow your business smarter, try Rentman free for 30 days. No credit card required.
FAQ
Frequently asked questions
No items found.
Previous blog posts
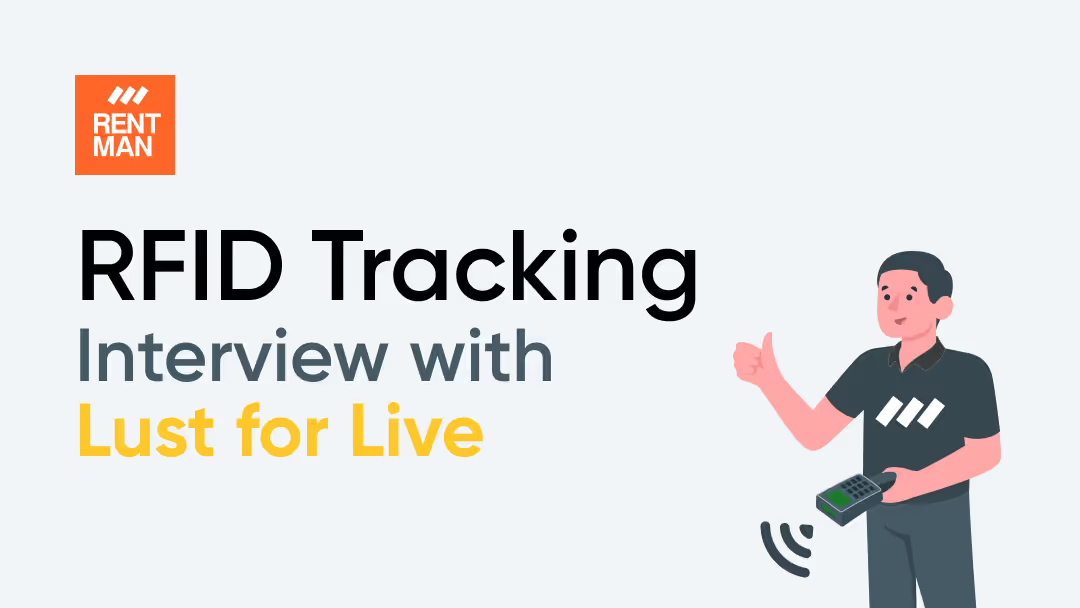
RFID - The next step in warehouse automation | Interview with Lust for Live
RFID - The next step in warehouse automation | Interview with Lust for Live
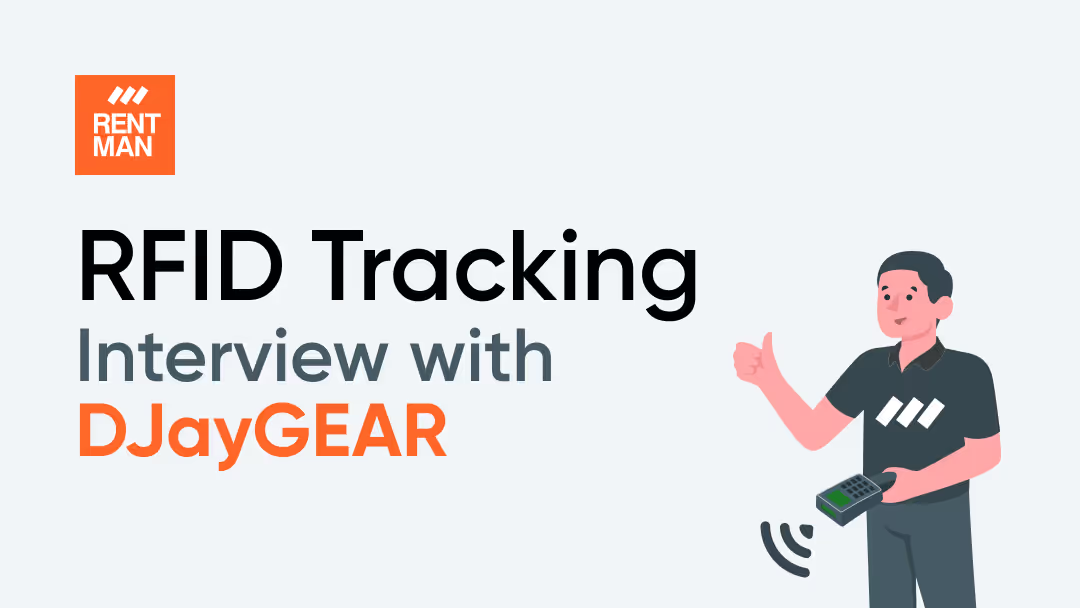
RFID - Is it enough to cover the risk of constantly losing equipment? Interview with DJayGEAR
RFID - Is it enough to cover the risk of constantly losing equipment? Interview with DJayGEAR
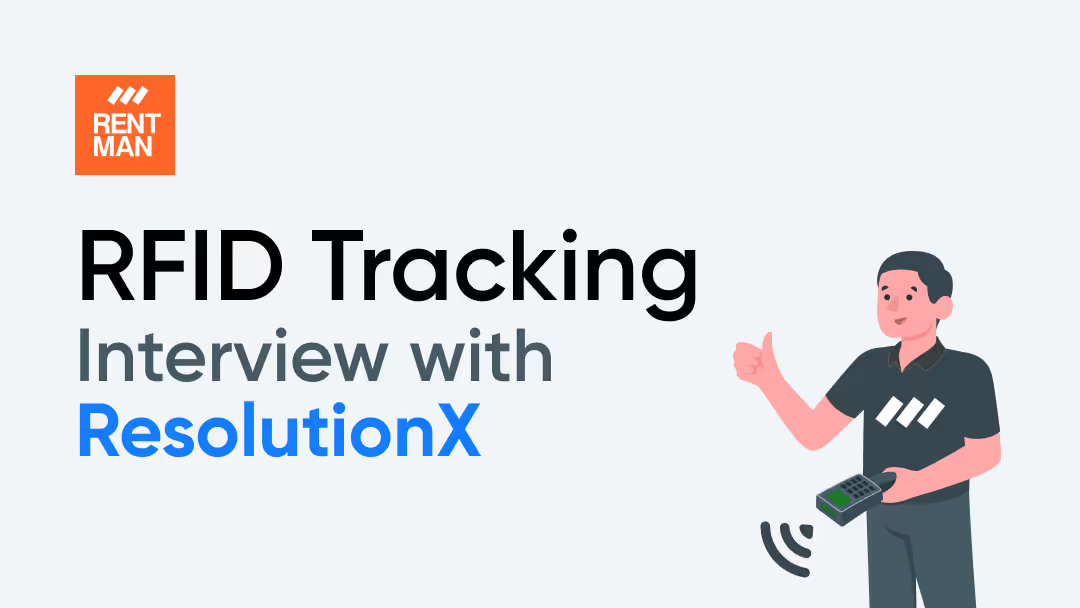