How to stop packing mistakes and equipment loss during high season
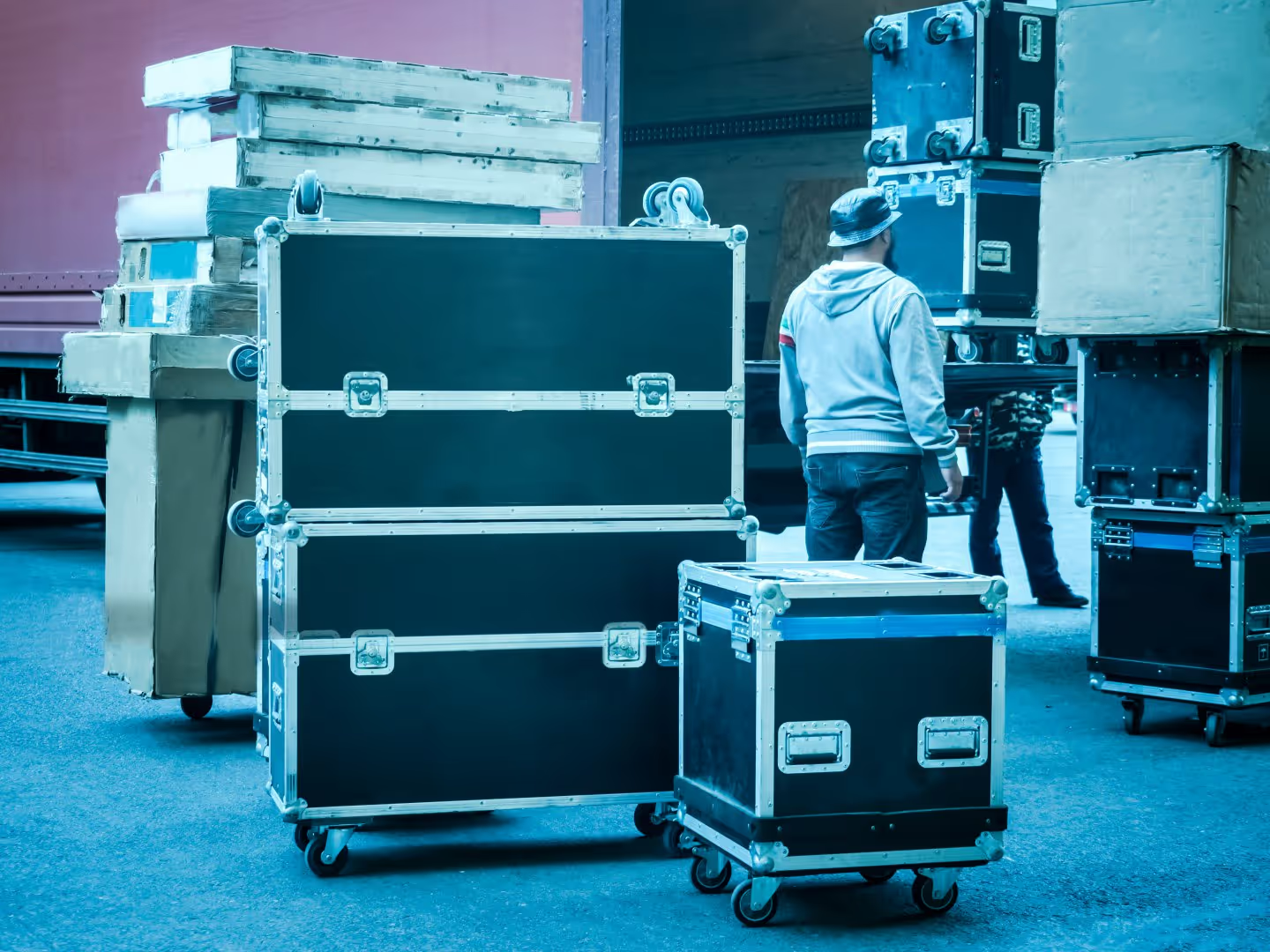
"Where's the amplifier rack? It was supposed to be in the van!" - Sounds familiar?
Especially during the chaotic summer months (including the months leading up to them), such scenarios can feel all too common. Packing the wrong gear, missing essential equipment, and losing gear post-event can cause major headaches - and most of all, ruin the reputation with your clients.
That’s why, in this article, we’ll dive into the nitty-gritty of common packing mistakes and equipment loss, explore why they happen in the first place, and discuss both offline and digital solutions to keep things running like a well-oiled machine.
1. Why packing mistakes occur in the first place
2. Why you need to act ASAP
3. Easy & quick offline solutions to prevent packing mistakes
4. Digitalize your processes - all in one place
Why packing mistakes occur in the first place
In order to know what you need to improve on, you need to understand what goes wrong first. Usually, the culprit shouldn’t be that hard to find. Tip: look for outdated methods or untrained staff.
Outdated methods: Using whiteboards, spreadsheets, and printed packing slips might have worked in the past, but during the high season, they become the reason for cluttered chaos. That’s because manual updates most likely lead to inconsistency in information and make it easy for items to be packed incorrectly or missed altogether. These old-school methods lack real-time synchronization, which is really important during peak times when quick changes and updates happen frequently. The lack of one, central system, means that multiple people might be working off different versions of the same document, leading to confusion and errors…
New and inexperienced staff: High season also means bringing in extra hands (often freelancers who might not be familiar with your packing processes). These new crew members can make rookie mistakes if they’re not properly trained. Without a clear understanding of your processes, the whereabouts of all equipment, and the importance of accuracy, new staff can easily overlook key packing steps.
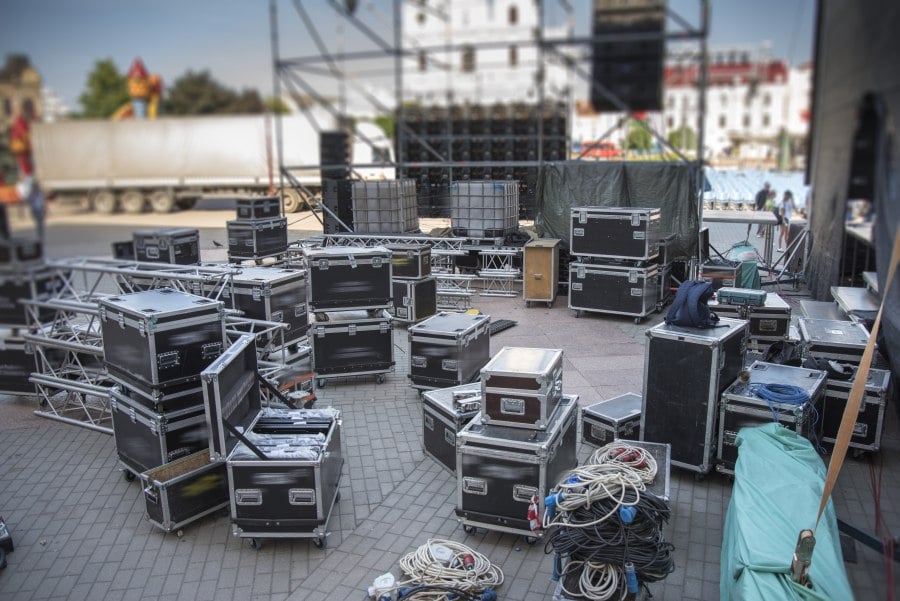
Why you need to act ASAP
If you've identified any of these issues, you’ll want to move fast! Incorrect packing can throw off setup times, causing a domino effect of delays that disturb your entire event schedule. Clients expect perfection, so any packing mistake, minor or big, can lead to dissatisfaction and harm your reputation. And not just that… your wallet will suffer too: these errors can lead to last-minute purchases or subrentals, often at a higher price than if you booked in advance. The financial impact of these mistakes can quickly add up.
It’s time to make some changes happen.
Easy & quick offline solutions to prevent packing mistakes
Let’s take a look at some offline strategies that you can implement today already - no excuse!
Boost teamwork and training: Regular training sessions will guarantee that everyone understands your packing process. Here, it’s important to prioritize accuracy over speed: make sure every item is checked and double-checked. Also consider implementing a buddy system where experienced staff mentor newcomers can be an effective way to ensure new employees quickly learn inside tips and tricks. And at last: create an environment of open communication and a culture where questions are welcomed and mistakes are used as learning opportunities.
Fix your documentation: Always make sure to update your inventory changes immediately - whether it’s a repair, new purchase, or disposal. Keeping a detailed and up-to-date inventory not only helps in accurate packing but also helps with tracking the condition and availability of equipment. In doing so, you will avoid renting out or scheduling equipment that is broken or not even available.
Organize your physical storage space: Clear organization is key to preventing packing mistakes. Here are a few methods to achieve that:
- Clear labeling: Clearly label all your shelves and storage areas. Dedicate specific spots for different types of equipment. For this, use large, easy-to-read labels that include both text and images.
- Color-coded systems: Implement a color-coded system for different categories of equipment. This can simplify the packing process and reduce the chances of packing the wrong items.
- Designated packing zones: Create designated zones for packing different types of equipment. This helps maintain order and makes sure that each item is packed correctly.
- Regular clean-ups: Schedule regular clean-up sessions to keep the storage area organized and free of clutter. This reduces the risk of items being misplaced or overlooked.
- Packing checklists: Provide detailed checklists for each packing job. Crew members should check off items as they pack them to make sure nothing is being overlooked.
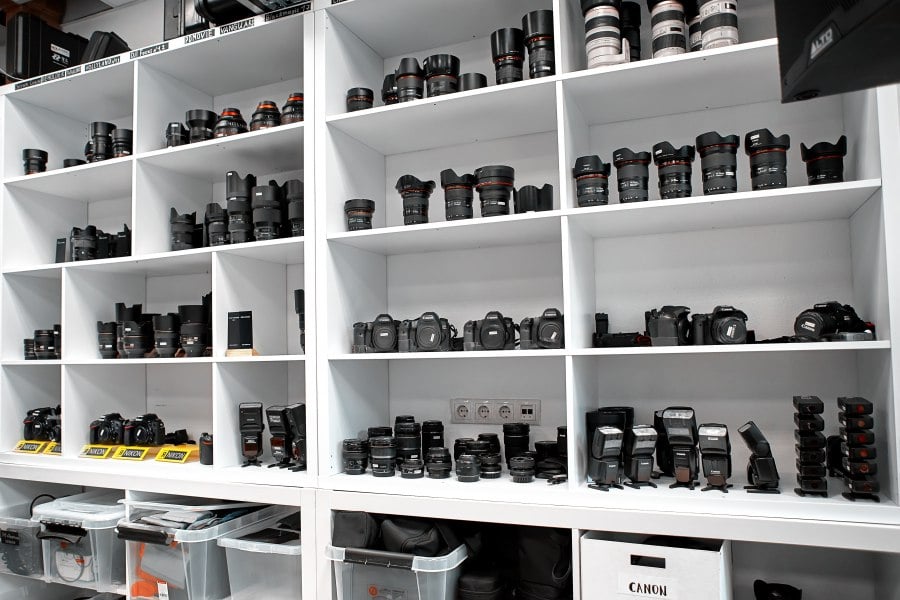
Digitalize your processes - all in one place
To eliminate packing mistakes, lost gear, and stress, we highly recommend centralizing your operations digitally.
Achieve 99.9% accuracy by using RFID technology
RFID technology allows your crew members to scan and process hundreds of items in seconds without individual scans. This quick scanning capability will make sure that the correct items and amounts leave the warehouse. If any items go missing, crew members will be immediately alerted!
Use the cloud
We recommend you always use a cloud-based platform: a real-time, always-synced center that keeps your entire team in the loop. Last-minute changes? No problem. Updates are instantly visible, ensuring everyone’s on the same page - all the time.
Rentman: an all-in-one software solution
There’s no need to buy different RFID technology, or download multiple cloud apps on your devices to guarantee success. Our software addresses all the critical needs of modern-day warehouse management by using fool-proof features, including:
- Digital packing slips: Streamline your packing process with digital slips that are always up-to-date.
- QR code scanning: Use Zebra scanners or mobile phones to quickly and accurately scan items.
- Increased traceability: Assign specific serial numbers to items, ensuring the correct products are packed.
- RFID tracking: Achieve near-perfect accuracy by scanning hundreds of items in seconds.
- Real-time equipment tracking: Keep everyone informed with cloud-based updates that reflect any changes instantly.
- Cloud-based software: Ensure that all team members, from crew to warehouse managers, have access to the latest information at all times.
The end result? Smooth operations that let you focus on what you do best: creating unforgettable events.
FAQ
Frequently asked questions
No items found.
Previous blog posts
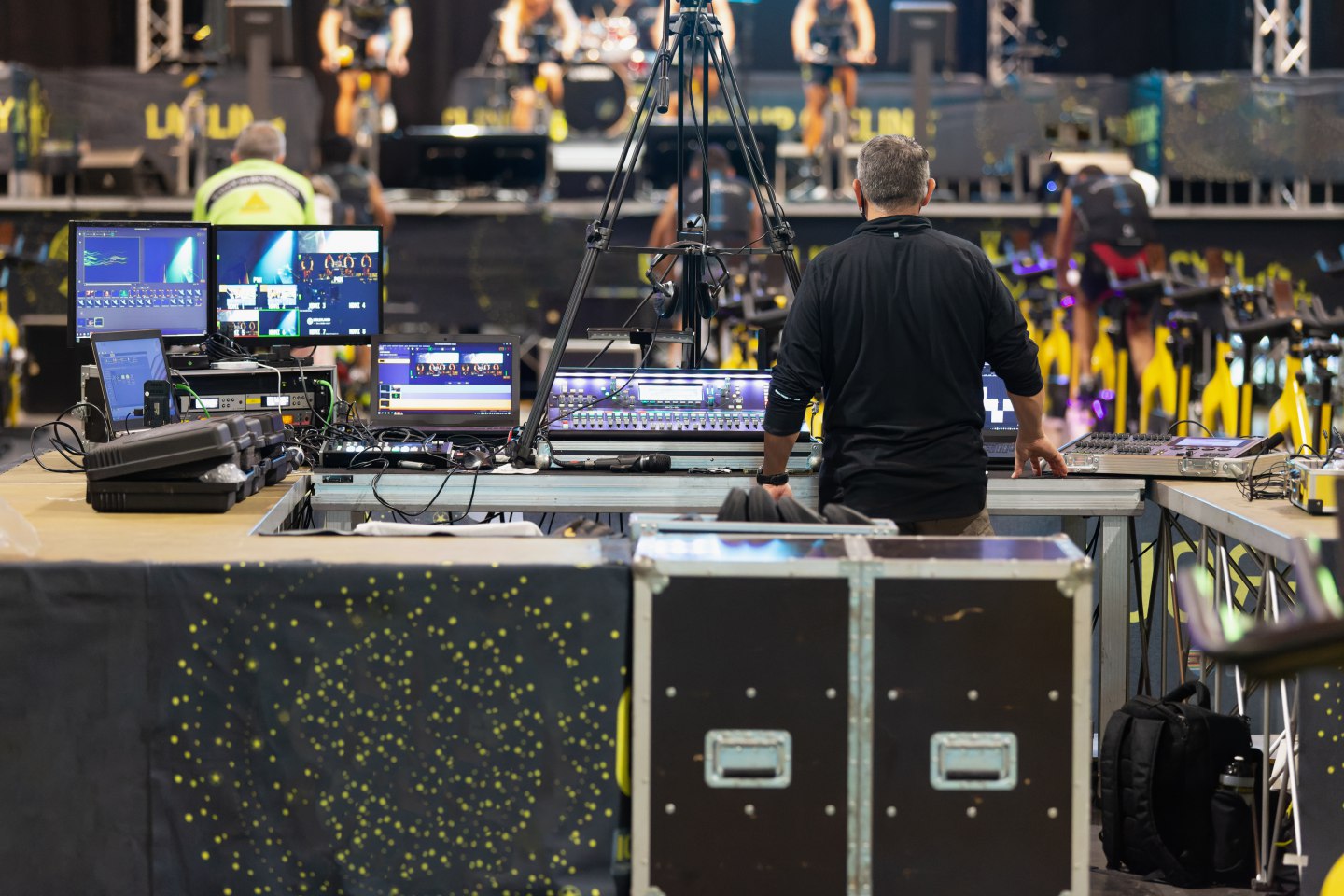
How to Eliminate Mistakes and Reduce Costs with Streamlined Crew Communication
How to Eliminate Mistakes and Reduce Costs with Streamlined Crew Communication
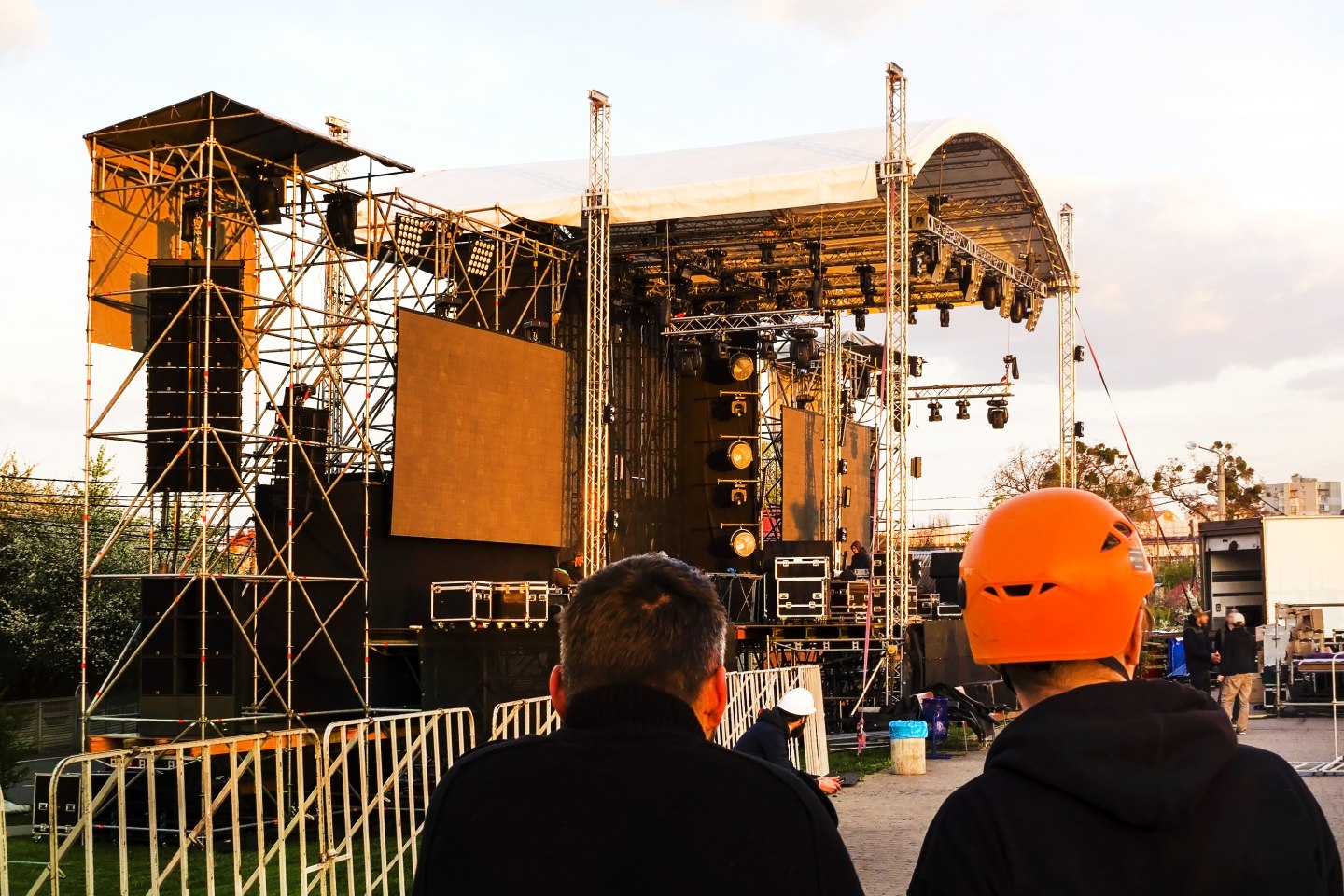