How to Manage your Inventory during High Seasons
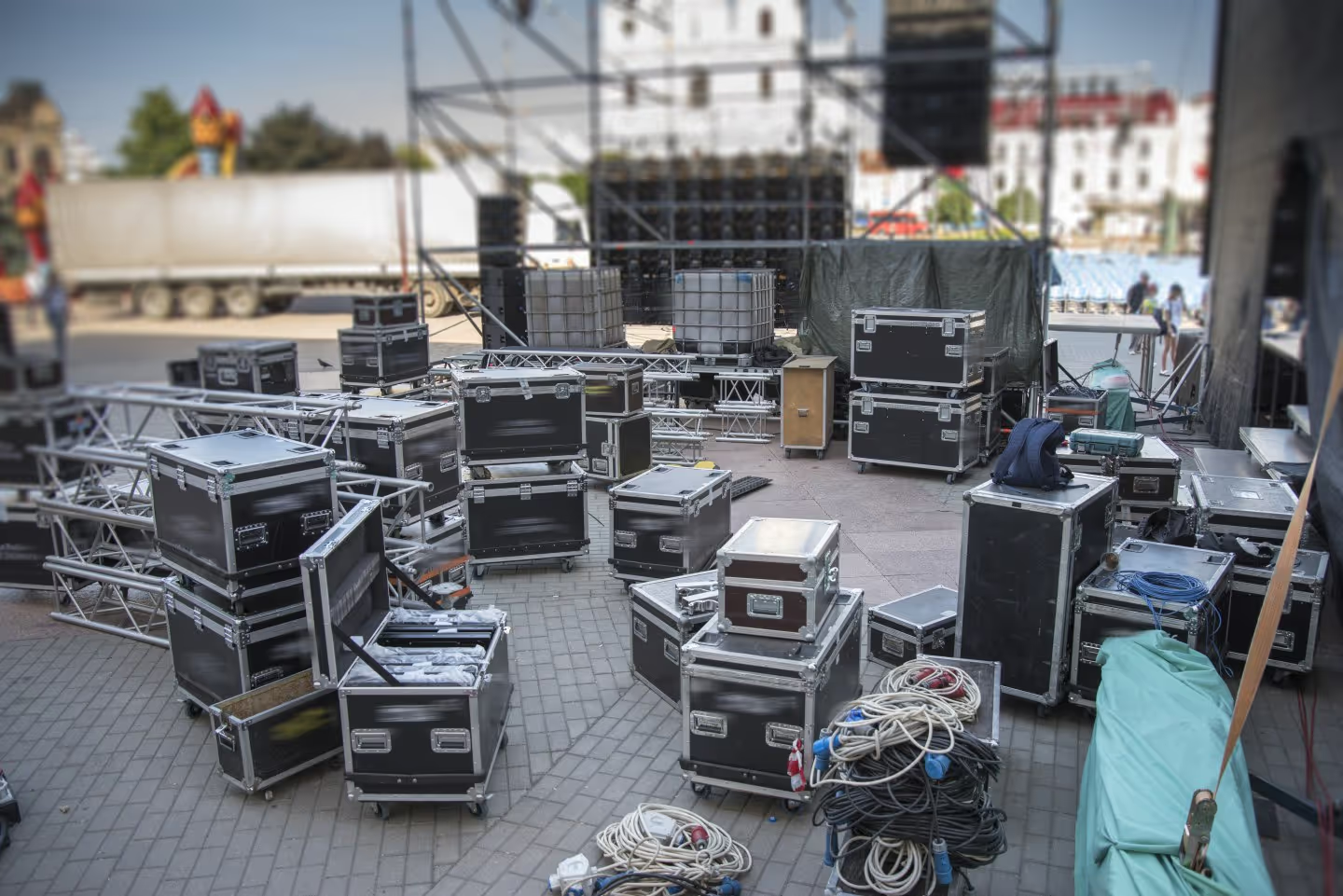
As the days grow longer and temperatures rise, so too does the inventory activity in the event industry. For example, between January and July 1st 2024, we saw an 182% increase in number of items being booked (scanned) and prepped for a production!
Dubbed as the 'high season', these months contrast heavily with the quieter times in the year that should serve as a period for planning, reflection and reorganization (more on that later). And while the high season can be a boon for business, it also brings a set of logistical challenges - particularly when it comes to managing inventory.
That’s why, in this article, our team of experts take you through the best practices for inventory management. So you can focus on what’s really important: facilitating unforgettable events.
1. Key challenges to be aware of
2. 6 Tips to manage your inventory like a pro
3. Prepping in low means flourishing in high
Key challenges to be aware of
Before we dive into the how’s, let’s explain the why’s first - the typical mess-ups that can happen when you're trying to keep up with the chaos of high season:
Packing fails: One wrong move in packing can set off a domino effect of delays and extra costs. Forgetting a crucial piece of audio equipment could lead to a last-minute, expensive replacement or result in a performance that doesn't meet client expectations.
Losing track of equipment: With the amount of events and equipment moving in and out, it’s easy to lose track of inventory. This can lead to double booking gear or, even worse, not having what you need for a big event. Talk about a nightmare…
Rookie mistakes: High season often means you need extra hands on deck, which usually involves bringing in new crew members. Getting them up to speed with your inventory system and handling all the tech without causing a disaster? That’s a challenge in itself.
6 Tips to manage your inventory like a pro
As it actually counts for many things in life: preparation is key. So without further ado, here are our top 6 recommended steps that will help you pave the way for smoother operations:
#1 Clean and prepare before the rush
The low season is the perfect time to roll up your sleeves and dive into maintenance and inspections. Control each piece of equipment for wear and tear, perform necessary repairs, and replace any gear that’s past its prime. By making sure that all your gear is in top-notch condition, you’ll avoid the hassle of last-minute malfunctions in high season.
#2 Keep the inventory count in check
Sort out your storage, so everything is easy to find and ready to roll out. A few ways you can do this:
- Start by labeling each shelf clearly and creating dedicated spaces for different types of equipment.
- Make sure the pathways in your storage area are clear to avoid any obstacles or accidents during pick-ups and drop-offs.
- A well-documented inventory that includes details like serial numbers, condition reports, and location can dramatically reduce the time spent searching for items and help prevent loss and theft.
#3 Optimize your inventory systems
Make it a habit to regularly review and update your inventory, especially during slower periods:
- Accurate data management: Use software or spreadsheets to keep your inventory records accurate and up-to-date. This prevents issues like double bookings and ensures you can always meet client needs without delay.
- Proactive maintenance: Schedule maintenance checks and repairs during slower times - based on the insights you gather from regular inventory reviews. This way, you’ll avoid equipment failures during moments you need them the most.
- Resource allocation: Analyze the usage patterns to better allocate equipment for all upcoming events and to make smarter purchasing decisions to meet different client demands.
#4 Staff training
As expect, you will need more hands on deck in high seasons. Start the hunt for good people early and get them trained before things get crazy. Once hired, invest in comprehensive training programs that include hands-on sessions with your inventory systems. Having a solid crew ready can be the difference between smooth sailing and a total meltdown.
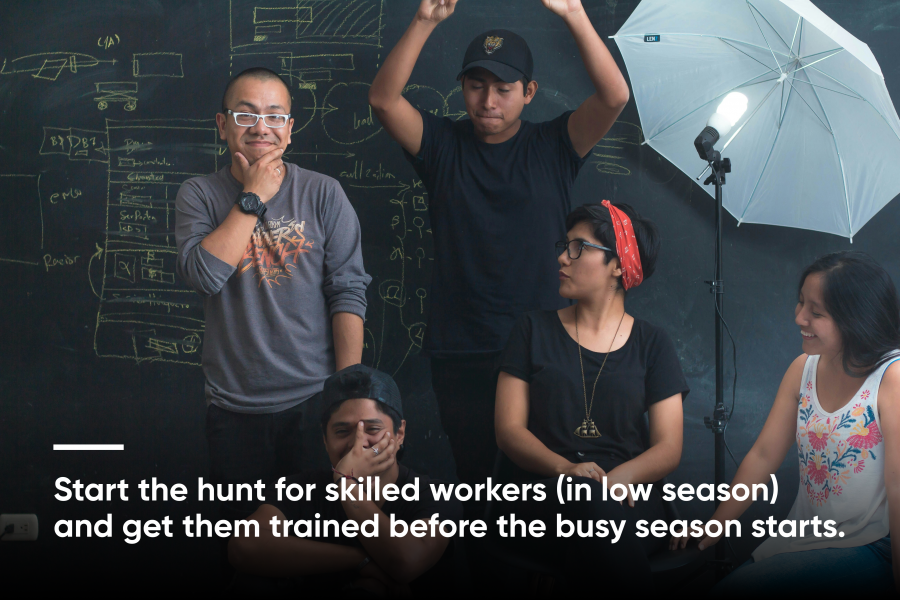
#5 Set up a tracking system for more expensive items
Keeping track of your high-value gear is super important to avoid losing stuff and keep things running smoothly. Using digital tracking software can make this a lot more efficient by showing you exactly where your equipment is and its status in real-time. Just make sure everyone on your team follows the same tracking steps so it’s consistent across the board. You can even step it up by tracking bulk items - which should be an easy-peasy task with the right tool.
#6 Choosing the right software solution
Ultimately, you’ll want to look for inventory management tools that do the heavy lifting for you (like updating your inventory levels and shipping statuses on the go). A platform like Rentman can be a lifesaver with features like digital packing slips, QR code scanning for fast and accurate packing, real-time equipment tracking, and a cloud-based setup that keeps everyone in the loop.
Prepping in low means flourishing in high
Prepping during the quieter months is going to be your best strategy for managing the chaos of high season. When you've taken the time to maintain your equipment, streamline your inventory system, and train your team thoroughly, you will be well-equipped to handle the demands that come with peak seasons.
By following these six tips, you can ensure that your inventory management process is as efficient and stress-free as possible,
Let's make this peak season your most successful yet!
FAQ
Frequently asked questions
No items found.
Previous blog posts
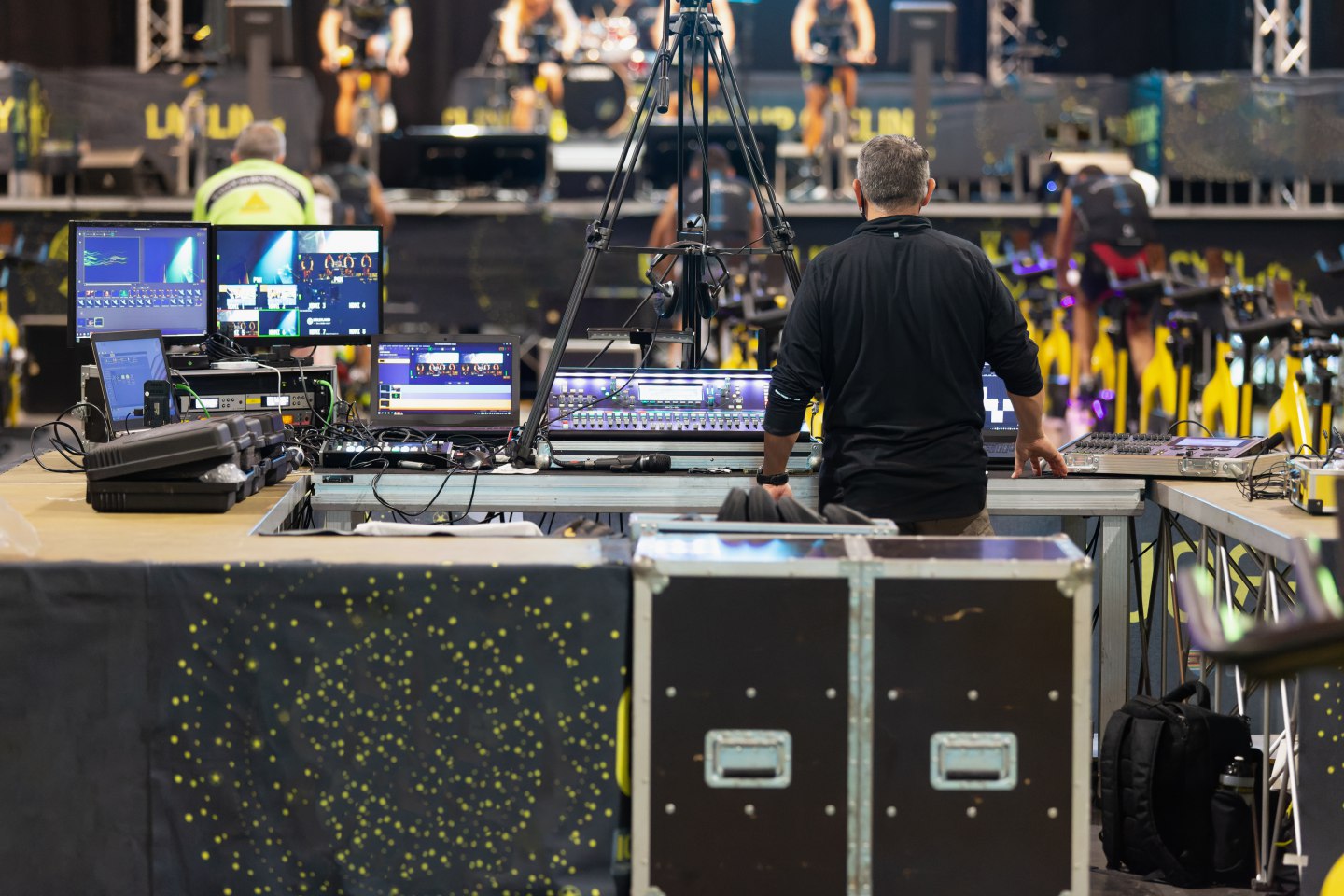
How to Eliminate Mistakes and Reduce Costs with Streamlined Crew Communication
How to Eliminate Mistakes and Reduce Costs with Streamlined Crew Communication
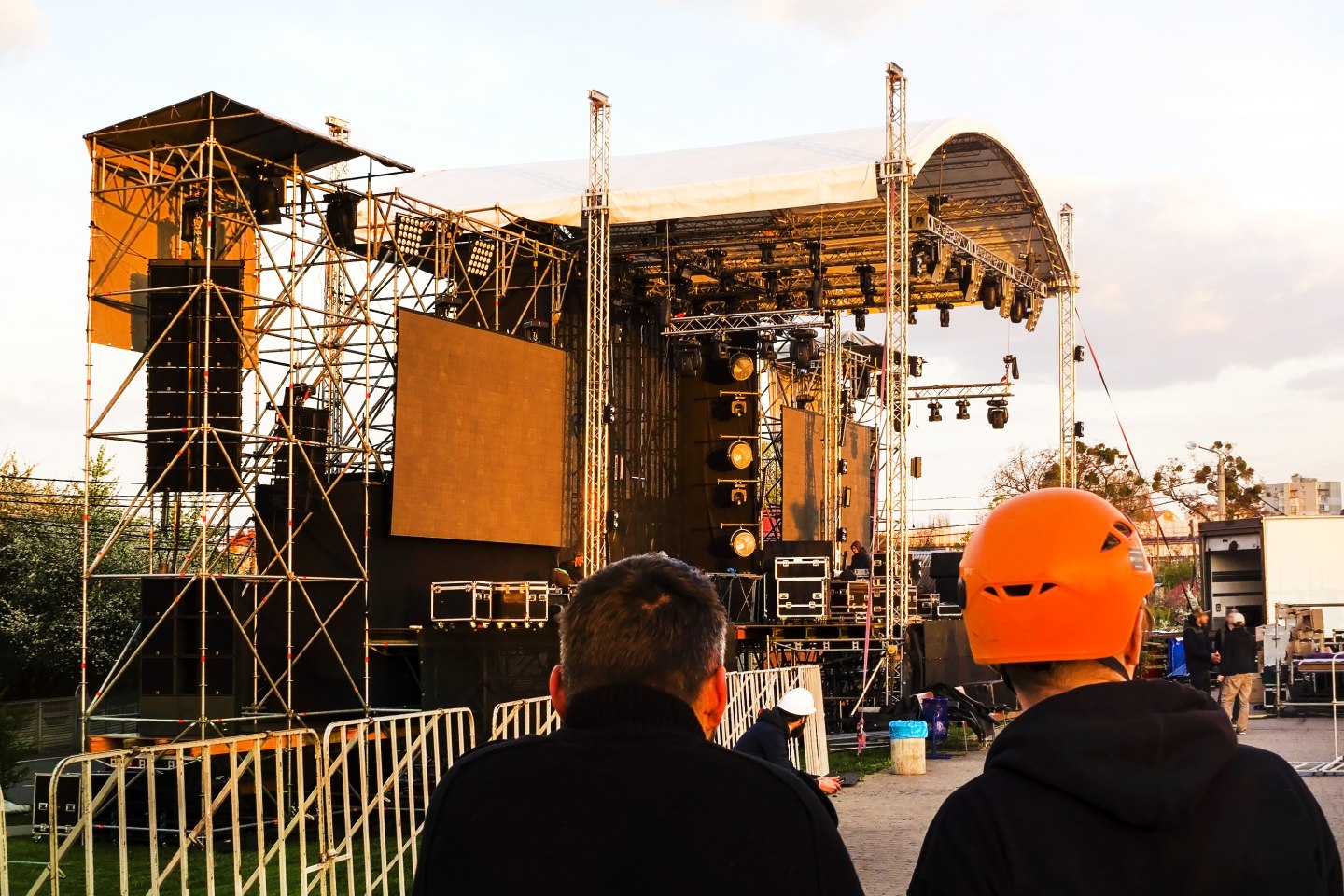
How to Streamline Crew Communication for Efficiency and Increased Crew Happiness
How to Streamline Crew Communication for Efficiency and Increased Crew Happiness
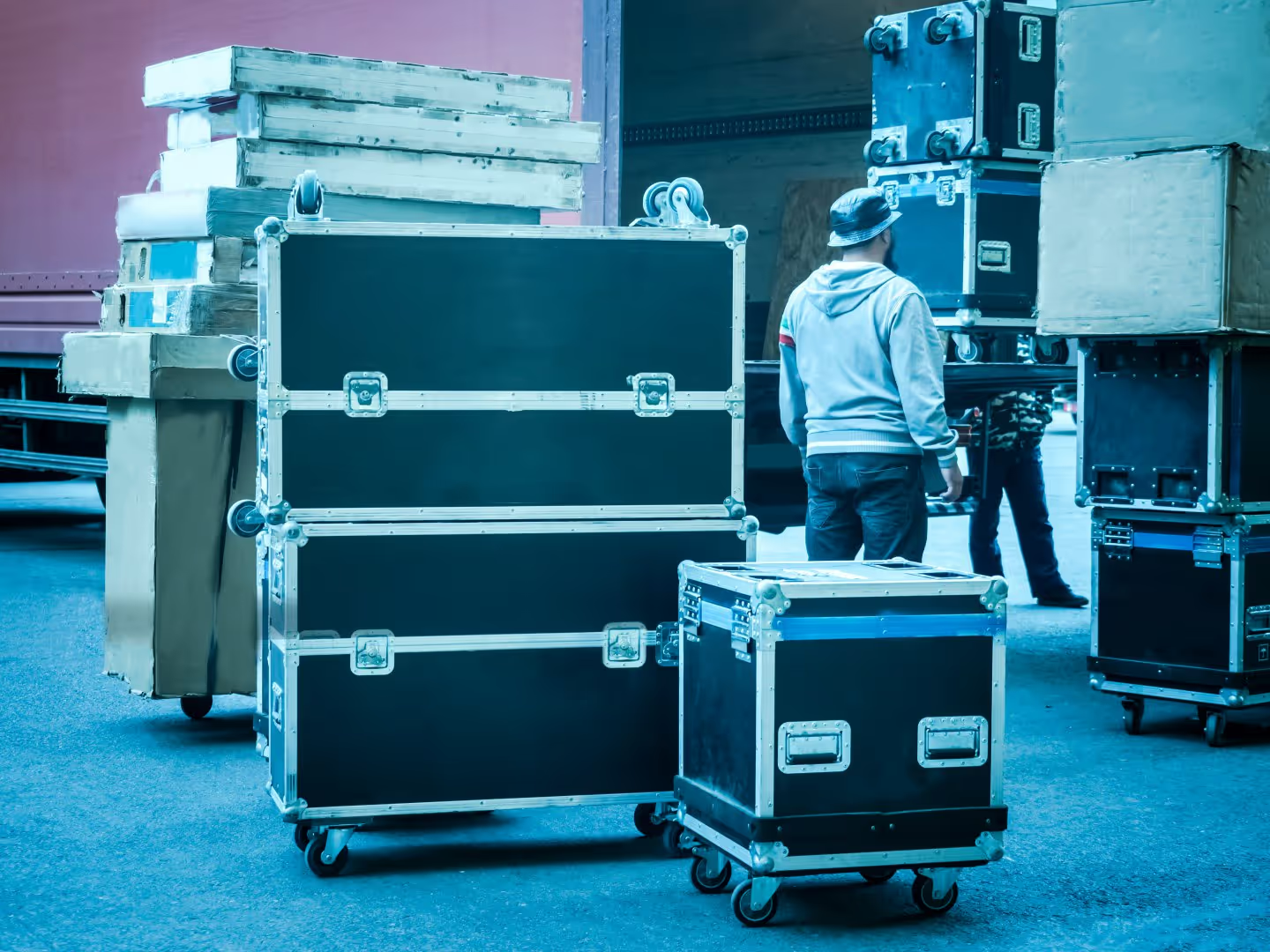