Equipment Inventory Management Software
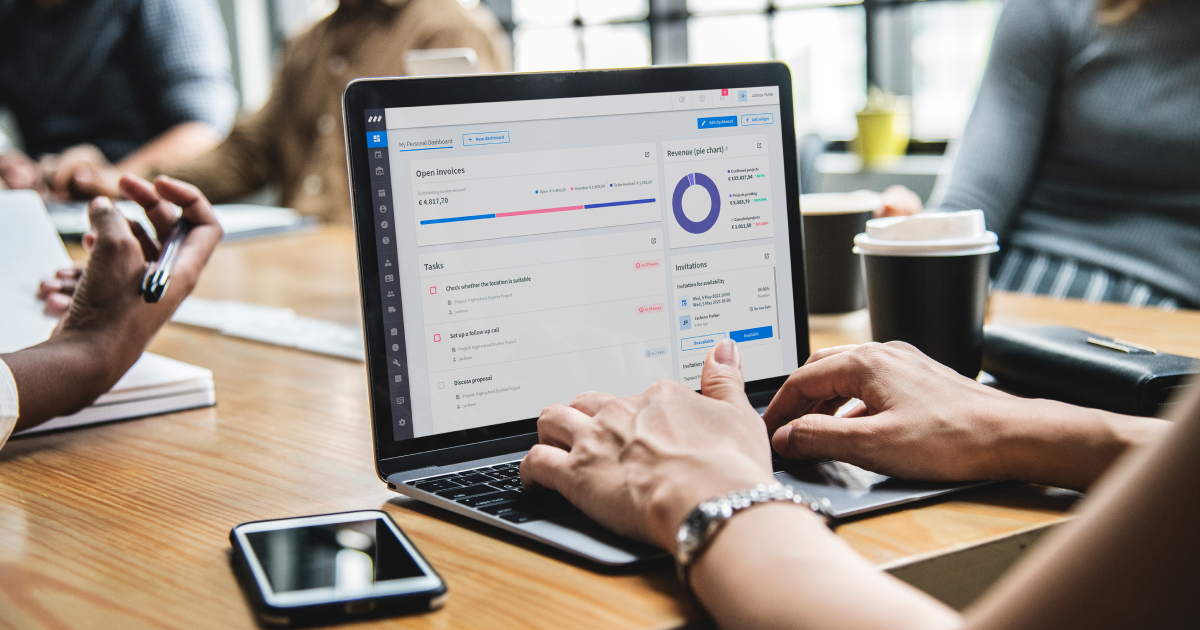
Managing equipment inventory can be a daunting task without the right tools, but equipment tracking software simplifies this process, ensuring efficiency and accuracy.
This software is designed to help businesses manage assets, track their equipment, monitor usage, and schedule maintenance, all from a centralized system.
By utilizing equipment inventory management software, companies can reduce downtime, prevent loss, and optimize resource allocation.
In this guide, we will delve into the key features, benefits, and considerations when selecting equipment inventory management software, helping you make an informed decision for your business needs.
1. Introduction to Asset Management Software
2. Key Features
3. Implementing the Software
4. Best Practices
5. Future Trends
Introduction to Asset Management Software
Why You Need It
Managing equipment manually is not only time-consuming but also prone to errors. Equipment tracking software provides a streamlined solution to these problems.
By automating asset tracking, the software helps ensure that all equipment is accounted for and in good working condition. This reduces the risk of losing high-value assets and minimizes downtime caused by equipment failure.
Additionally, the software offers real-time asset data and analytics, allowing businesses to make data-driven decisions about asset management across their day-to-day operations.
Whether you are a small business or a large enterprise or company, investing in equipment inventory management software can lead to significant cost savings and improved operational efficiency.
Key Benefits Overview
Equipment inventory management software offers several key benefits that can transform your business operations. Firstly, it enhances accuracy by automating asset tracking and data entry, reducing human error.
Secondly, it improves efficiency with real-time insights into equipment status, availability, and maintenance schedules. This helps in preventing unexpected downtime and prolonging the lifespan of your assets.
Thirdly, it optimizes resource allocation by providing data-driven insights, ensuring that equipment is utilized effectively and not left idle. Furthermore, the software can help in compliance management by maintaining accurate records of equipment inspections and certifications for all your assets.
In summary, using equipment inventory management software can lead to cost savings, better decision-making, and more streamlined day-to-day operations.
Common Challenges Solved
Equipment inventory management software addresses several common challenges faced by small businesses. One major issue is the misplacement or loss of equipment, which can be costly. The software provides accurate asset tracking and location data, reducing the likelihood of tools going missing.
Another challenge is the inefficiency in scheduling maintenance. With automated alerts and reminders, the software ensures timely servicing, thereby preventing unexpected breakdowns.
Additionally, manual record-keeping can lead to errors and inconsistencies. The software streamlines data entry processes, maintaining accurate and up-to-date records on all your assets.
Finally, managing compliance with industry regulations can be complex and time-consuming. Equipment inventory management software simplifies this by keeping detailed records of inspections and certifications, ensuring that you meet all regulatory requirements for your assets.
Key Features
Real-Time Asset Tracking Capabilities
Real-time tracking is one of the standout features of equipment inventory management software. This functionality allows businesses to monitor the location and status of their equipment instantaneously.
Using technologies like QR-code tracking, barcode scanning and RFID, the software provides precise data on where each piece of equipment is at any given moment. This not only helps in preventing loss but also aids in efficient resource allocation.
For instance, if a piece of equipment is underutilised, managers can reassign it to areas where it is needed most. Real-time tracking software also enables quick responses to issues, such as equipment malfunctions or unexpected downtime, by alerting the relevant personnel immediately.
Overall, the ability to manage assets and monitor equipment in real-time enhances operational efficiency and asset utilisation, making it an invaluable feature for any business.
Automated Reporting Functions
Automated reporting functions are a crucial component of equipment inventory management software. These features allow businesses to generate detailed reports on various aspects of equipment management, such as usage, maintenance schedules, and operational efficiency.
By automating the reporting process, the software eliminates the need for manual data compilation and analysis, saving time and reducing the risk of human error.
Managers can easily access customised reports to gain insights into equipment performance and identify areas for improvement. Additionally, automated reporting ensures compliance with industry standards by maintaining accurate and up-to-date records of inspections and certifications.
This functionality not only aids in decision-making but also enhances transparency and accountability within the organisation.
By leveraging automated reporting, businesses can make data-driven decisions that optimise resource allocation and improve overall efficiency.
User-Friendly Interface
A user-friendly interface is essential for the effective utilization of equipment inventory management software (asset management tool or platform).
The software should be intuitive and easy to navigate, allowing users to quickly access the information they need about their assets without extensive training. A well-designed interface includes clear menus, simple icons, and straightforward commands, making it accessible to users of all technical skill levels.
This ease of use reduces the learning curve and enhances productivity, as employees can focus more on their tasks rather than struggling with complicated software.
Additionally, a user-friendly interface often features customizable dashboards using custom reports, enabling users to tailor the display according to their specific needs and preferences. This personalization further improves efficiency by highlighting the most relevant data and tools for day-to-day operations.
Ultimately, an intuitive interface ensures that the equipment tracking software is adopted smoothly across the organization, maximizing its benefits and ensuring a higher return on investment for your overall asset management solution.
Implementing the Software
Initial Setup Guide
Setting up equipment inventory management software involves several key steps to ensure a smooth implementation. First, conduct a comprehensive inventory audit to document all existing equipment, including serial numbers, locations, and current conditions. This initial data will form the foundation of your new asset management system.
Next, configure the software to align with your business needs. This includes setting up categories for your various assets, defining user roles, and customizing reporting templates. Once the configuration is complete, import your audited data into the software. Most platforms offer import tools to facilitate this process.
After the data import, it's crucial to train your team on how to effectively use the equipment tracking system. Provide hands-on training sessions and create user manuals for reference. Finally, perform a trial run to identify any potential issues and make necessary adjustments to your asset management software.
By following these steps, you can ensure a successful setup and maximize the benefits of your equipment inventory management software.
Crew Training Tips
Effective crew training is crucial for the successful implementation of equipment inventory management software. Begin by organizing comprehensive training sessions that cover all aspects of the software, from basic navigation to advanced features relevant to asset management.
Use a combination of instructional methods, such as live demonstrations, hands-on exercises, and video tutorials, to cater to different learning styles. Encourage staff to ask questions and provide feedback to ensure they understand the material thoroughly.
Additionally, create user manuals and quick-reference guides that employees can consult as they become familiar with the software for managing their assets.
It's also beneficial to designate super users or champions who can provide ongoing support and training to their colleagues on the new asset management tool. Regularly schedule follow-up sessions to address any issues and introduce new features or updates to the software.
By investing time in thorough training, you can ensure that your team is confident and proficient in using the equipment inventory management software, leading to increased efficiency and smoother day-to-day operations in asset management.
Integration with Existing Systems
Integrating your new equipment inventory management software with existing systems is essential for streamlining operations and ensuring data consistency across your asset management tools.
Start by assessing the compatibility of the software with your current IT infrastructure, including ERP systems, accounting software, and other tools relevant to asset management. Opt for software solutions that offer API capabilities or built-in integration features to support and facilitate seamless data exchange.
During the integration process, establish clear protocols for data synchronization to avoid discrepancies within your asset management system. It's also vital to involve your IT team to oversee the technical aspects and troubleshoot potential issues.
Conduct thorough testing to ensure that the integrated systems communicate effectively and that data flows smoothly between them for your asset management needs. Proper integration not only enhances operational efficiency but also provides a unified view of your assets across different platforms.
This holistic approach enables better decision-making and optimises resource management, ultimately contributing to the overall success of your operations, your equipment inventory management system and overall asset management strategy.
Best Practices
Regular System Updates
Keeping your equipment inventory management software up to date is crucial for maintaining its efficiency and security. Regular system updates often include important patches that fix bugs and vulnerabilities, protecting your data from potential threats.
Additionally, updates can bring new features and improvements that enhance the software's functionality and user experience. To ensure you don't miss any updates, enable automatic updates if the software allows, or schedule regular checks for new versions.
It's also a good practice to back up your data before performing any updates to safeguard against potential data loss. Involve your IT team in the update process to handle any technical issues that might arise.
Regularly updating your software ensures that it remains aligned with the latest industry standards and technological advancements, thereby maximising the benefits and longevity of your equipment inventory management system.
Data Backup Strategies
Implementing robust data backup strategies is essential for safeguarding the information stored in your equipment inventory management software.
Start by establishing a regular backup schedule that suits your business needs, whether daily, weekly, or monthly. Utilise both on-site and off-site backup solutions to ensure redundancy.
Cloud-based backups offer additional security and accessibility, allowing you to retrieve data even in the event of physical disasters. Ensure that your backup process includes all critical data, such as equipment details, maintenance records, and user logs.
Automate the backup process where possible to minimise the risk of human error. Regularly test your backup system to verify that data can be restored successfully and that no information is missing or corrupted.
Keeping multiple backup copies and periodically reviewing your backup strategy can provide added assurance that your data is secure, reliable, and easily recoverable in case of any unforeseen incidents.
Analysing Usage Reports
Regularly analysing usage reports generated by your equipment inventory management software can provide valuable insights into your operations. These reports offer detailed information on equipment utilisation, maintenance schedules, and performance metrics.
By reviewing this data, you can identify patterns that indicate underused or overused assets, helping you make informed decisions about resource allocation. Look for trends that may suggest the need for additional training or process improvements.
Monitoring maintenance reports can also help you anticipate potential equipment failures, allowing you to schedule preventive maintenance and reduce downtime. Additionally, usage reports can highlight compliance with industry regulations and internal policies, ensuring that all equipment meets necessary standards.
Utilise these insights to optimise your inventory management strategy, improve operational efficiency, and reduce costs. Regularly scheduled report analysis can provide a continuous feedback loop, with real time data enabling you easily track how to adjust and refine your approach as needed for optimal results.
Future Trends
AI and Machine Learning
Artificial Intelligence (AI) and Machine Learning (ML) are set to revolutionise equipment inventory management software. These technologies can enhance predictive maintenance by analysing vast amounts of data to forecast potential equipment failures before they occur.
This proactive approach reduces downtime and extends the lifespan of assets. AI-driven analytics can also optimise inventory levels by predicting future equipment needs based on historical data and usage patterns.
Machine learning algorithms can offer more accurate asset valuations and depreciation forecasts, aiding in better financial planning. Additionally, AI can automate repetitive tasks, such as data entry and report generation, freeing up human resources for more strategic activities.
As these technologies continue to evolve, they will provide deeper insights and more efficient solutions, making equipment inventory management smarter and more effective.
Adopting AI and ML in your inventory management strategy can significantly improve operational efficiency and drive long-term business success.
Mobile Integration
Mobile integration is becoming increasingly important in the future of equipment inventory management software. With mobile access, employees can update and retrieve inventory data in real-time, regardless of their location.
This flexibility is particularly beneficial for field technicians and remote workers who need immediate access to equipment information. Mobile apps can facilitate tasks such as barcode scanning or QR-code tracking, conducting inspections, and reporting issues directly from a smartphone or tablet. This streamlines processes and reduces the likelihood of errors associated with manual data entry.
Additionally, mobile integration supports instant communication and collaboration, allowing teams to coordinate more effectively. Push notifications and alerts can keep staff informed about maintenance schedules, equipment status updates, and other critical information.
As mobile technology continues to advance, it will play an increasingly vital role in enhancing the efficiency and responsiveness of equipment inventory management systems. Embracing mobile integration can lead to improved productivity, accuracy, and overall operational effectiveness.
Enhanced Security Measures
Enhanced security measures are becoming a critical focus in the future development of equipment inventory management software. As cyber threats continue to evolve, protecting sensitive inventory data is paramount.
Advanced encryption techniques are being implemented to secure data both at rest and in transit. Multi-factor authentication (MFA) adds an additional layer of security, ensuring that only authorised personnel can access the system.
Role-based access controls further limit exposure by granting permissions based on user roles and responsibilities. Regular security audits and vulnerability assessments help identify and mitigate potential risks.
Additionally, real-time monitoring and alert systems can detect and respond to suspicious activities promptly. Cloud-based solutions are also adopting stringent compliance standards to meet industry regulations and protect user data.
By incorporating these enhanced security measures, equipment inventory management software can offer robust protection against data breaches and unauthorised access, ensuring the integrity and confidentiality of your valuable asset information.
FAQ
Frequently asked questions
No items found.