Understanding Equipment Availability: Why It Matters for Your Business
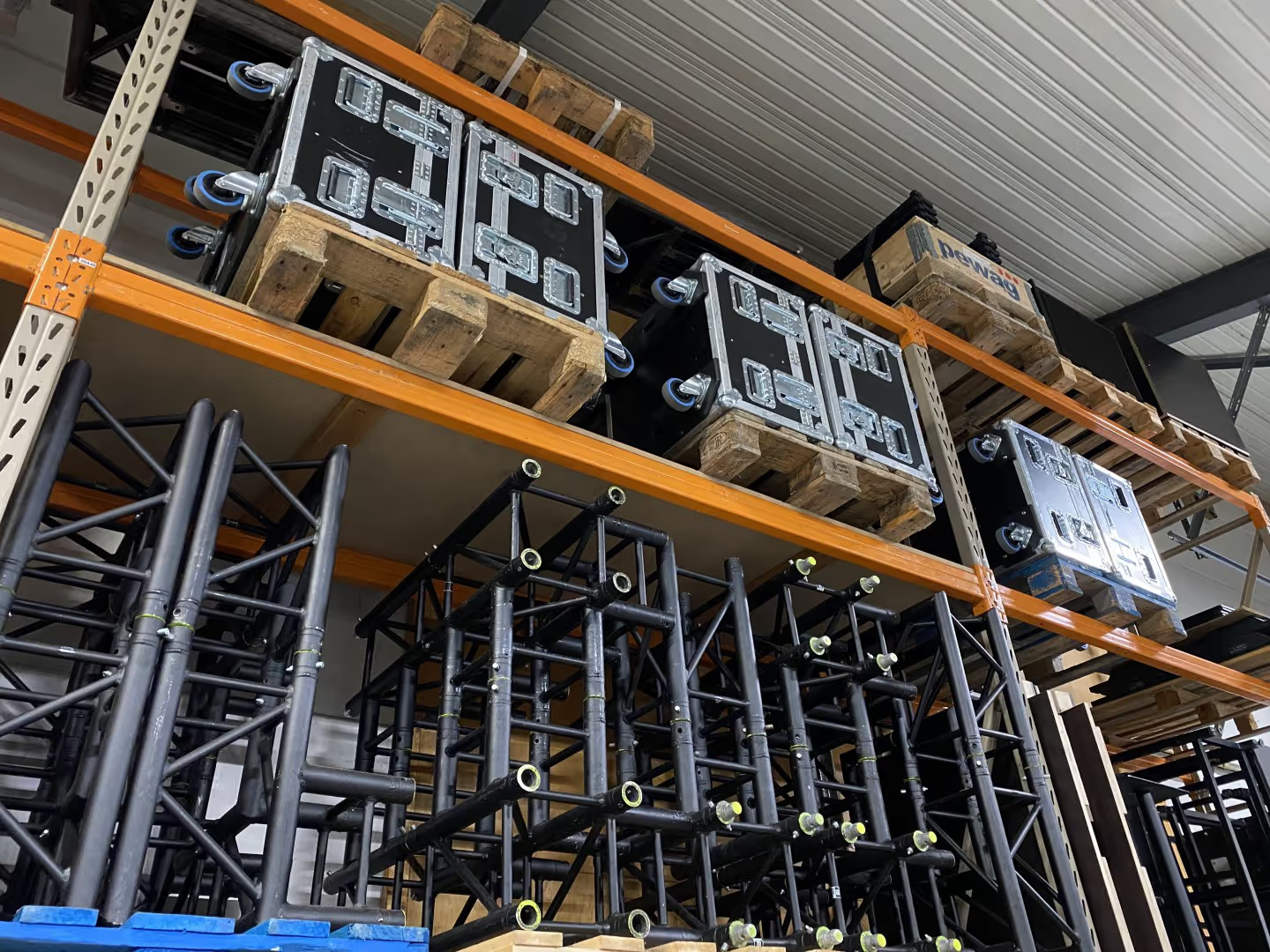
Equipment availability is a crucial factor that significantly impacts the efficiency and productivity of any business, especially those in the AV, Events, & Media Production industries. It refers to the proportion of time that equipment is in a condition to perform its intended function. When equipment is frequently unavailable due to breakdowns or maintenance, it can lead to operational delays and increased costs, affecting the overall profitability of the company. By understanding and optimizing equipment availability, businesses can ensure smoother operations, total downtime, reduce downtime, and ultimately enhance their bottom line. In this article, we will delve into the importance of equipment availability, its impact on business performance, and strategies to improve it effectively.
The Importance of Equipment Availability
Defining Equipment Availability
Equipment availability is a measure of the readiness of equipment to perform its intended tasks when required. It is calculated as the ratio of actual operating time to the total time the equipment is needed. This metric includes periods when equipment is operational and excludes downtime due to maintenance or failures. Understanding this concept helps businesses identify inefficiencies and potential areas for improvement in equipment effectiveness. By maintaining high equipment availability, companies can maximize production output and meet customer demands more reliably. A low availability rate might indicate frequent breakdowns or lengthy maintenance periods, which can disrupt workflow and increase costs. Thus, by focusing on equipment availability, businesses can enhance operational efficiency and ensure that their resources are being used effectively. Addressing equipment availability proactively can lead to better workforce planning and resource allocation, contributing to a more robust and resilient operational strategy.
Impact on Business Operations
Equipment availability directly influences business operations. When equipment is consistently available, it allows for smoother workflows and uninterrupted production processes. Conversely, low availability can lead to bottlenecks, delaying production schedules and impacting delivery timelines. This can result in unsatisfied customers and potential revenue loss. Furthermore, frequent equipment downtime can escalate operational costs due to overtime labor, expedited shipping, or replacement rentals. It also places a strain on maintenance teams and can increase the wear and tear on other equipment as they compensate for unavailable machinery. In industries where timing is critical, such as manufacturing and logistics, maintaining high equipment availability is essential. It ensures that operations remain efficient, predictable, and cost-effective. By prioritizing equipment availability, businesses can minimize disruptions, reduce operational risks, and maintain a competitive edge. This proactive approach overall equipment effectiveness supports sustainable growth and helps companies fulfill market demands consistently.
Real-World Examples
Consider the manufacturing sector, where equipment availability is vital for maintaining production quotas. A car manufacturer, for instance, relies on assembly lines that must function optimally around the clock. If a critical piece of machinery breaks down, it can halt the entire production line, leading to significant delays and financial losses. Similarly, in the healthcare industry, the availability of medical equipment can directly affect patient outcomes. Hospitals must ensure that diagnostic machines, like MRIs and CT scanners, are readily available to provide timely care. Another example where factors influence equipment availability is in the transportation sector, where airlines depend heavily on aircraft availability. A grounded plane due to maintenance issues can disrupt schedules and inconvenience passengers, affecting the airline's reputation and profitability. These examples underscore the importance of equipment availability across various industries. They highlight how maintaining high availability levels is crucial for ensuring operational efficiency and customer satisfaction.
Key Factors Affecting Availability
Maintenance and Repairs
Effective maintenance and timely repairs play a crucial role in ensuring high equipment availability. Regular maintenance helps prevent unexpected breakdowns by identifying and addressing potential issues before they escalate. This proactive approach includes scheduled inspections, routine servicing, and predictive maintenance strategies using data analytics. When equipment does require repairs, swift response and skilled technicians are essential to minimize downtime. Delays in equipment repairs can lead to extended periods of unavailability, disrupting operations and increasing costs. Additionally, having a well-organized spare parts inventory ensures that replacement components are readily available when needed, reducing the time equipment remains out of service. Investing in training for maintenance personnel can also enhance their ability to quickly diagnose and rectify issues, further improving equipment availability. By prioritizing maintenance and repairs, businesses can maximize equipment uptime, ensure consistent operational performance, and maintain a competitive advantage in their industry.
Supply Chain Issues
Supply chain issues can significantly impact equipment availability. Disruptions in the supply chain can lead to delays in obtaining essential parts needed for maintenance and repairs, causing extended equipment downtime. This is particularly critical in industries dependent on specialized components that may not have readily available alternatives. Global events, such as natural disasters or geopolitical tensions, can exacerbate these delays, affecting the entire operational flow. Additionally, fluctuations in demand can strain suppliers, leading to shortages or increased lead times for critical equipment components. To mitigate these risks, businesses must develop robust supply chain strategies. This includes building strong relationships with multiple suppliers, maintaining a stock of essential parts, and using technology to forecast demand and manage inventory effectively. By addressing supply chain vulnerabilities, companies can better ensure equipment availability, minimizing downtime, thereby sustaining their operational efficiency and meeting customer expectations without interruption.
Technological Advancements
Technological advancements are pivotal in enhancing equipment availability. Modern technology, such as the Internet of Things (IoT), artificial intelligence (AI), and machine learning, enables predictive maintenance. These technologies allow businesses to monitor equipment performance in real-time and predict potential failures before they occur. By anticipating maintenance needs, companies can schedule repairs at convenient times, minimizing disruptions. Additionally, advancements in automation and robotics can improve the precision and efficiency of maintenance tasks, further reducing equipment downtime. Implementing advanced diagnostic tools also helps maintenance teams and equipment operators quickly identify and resolve issues. Moreover, digital twins—virtual models of physical equipment—enable businesses to simulate scenarios and optimize maintenance schedules based on data-driven insights. Embracing these technological innovations not only improves equipment availability but also enhances overall operational efficiency. By staying at the forefront of technology, companies can maintain a competitive edge and ensure that their equipment remains reliable and productive.
Strategies to Improve Availability
Preventive Maintenance Programs
Implementing preventive maintenance programs is an effective strategy to reduce machine downtime and enhance equipment availability. Unlike reactive maintenance, which addresses problems after they occur, preventive maintenance focuses on regular, scheduled upkeep to prevent failures. This proactive approach involves routine inspections, cleaning, lubrication, and parts replacement based on usage patterns and equipment condition. By identifying wear and tear early, businesses can address potential issues before they lead to equipment downtime. Preventive maintenance helps extend the lifespan of machinery and reduces the likelihood of unexpected breakdowns, ensuring that equipment remains available when needed. This approach also allows for better planning and resource allocation, as maintenance activities can be scheduled during non-peak operational periods. Furthermore, keeping detailed records of maintenance activities and equipment performance helps refine and optimize these programs over time. By prioritizing preventive maintenance, companies can achieve higher equipment availability, improve operational reliability, and reduce overall maintenance costs.
Efficient Inventory Management
Efficient inventory management is vital for maintaining high equipment availability. Ensuring that all necessary spare parts and supplies are readily accessible minimizes downtime when equipment requires maintenance or repairs. By using inventory management systems, like Rentman, you can track stock levels, optimize maintenance strategies monitor usage patterns, and automate reordering processes. This helps prevent shortages and ensures that critical components are always on hand. Implementing just-in-time inventory practices can also reduce holding costs while maintaining readiness for unforeseen equipment needs. Plus, categorizing inventory based on criticality helps prioritize which parts need to be stocked more rigorously. Regular audits of inventory can identify slow-moving items and optimize stock levels accordingly. By aligning inventory management with maintenance schedules, companies can ensure that parts are available precisely when needed, thus reducing waiting times. Effective inventory management not only supports equipment availability but also contributes to cost savings and improved operational efficiency.
Employee Training and Development
Employee training and development are essential components in improving equipment availability. Well-trained staff can perform routine maintenance tasks efficiently and identify potential problems before they escalate. Regular training programs ensure that employees are up-to-date with the latest maintenance techniques and safety protocols, which is crucial for minimizing equipment downtime. Cross-training employees in multiple roles can also provide flexibility, enabling them to step in when specific expertise is needed. Investing in development programs fosters a deeper understanding of equipment operations, enhancing troubleshooting skills and reducing reliance on external technicians. Furthermore, empowering employees through continuous learning opportunities boosts morale and engagement, leading to a more proactive approach in maintaining equipment availability. Encouraging a culture of continuous improvement and innovation among staff can lead to creative solutions for further maximizing equipment availability and uptime. By prioritizing employee training, businesses can ensure a skilled workforce capable of supporting high equipment availability and overall operational success.
Measuring Equipment Availability
Key Performance Indicators
Key Performance Indicators (KPIs) are crucial for assessing equipment availability and identifying areas for improvement. Common KPIs in this context include Availability Rate, Mean Time Between Failures (MTBF), and Mean Time to Repair (MTTR). The Availability Rate measures the proportion of time equipment is operational compared to total scheduled time. MTBF indicates the average time equipment operates without failure, highlighting reliability. In contrast, MTTR measures the average time taken to repair an equipment failure, reflecting maintenance efficiency. Monitoring these KPIs helps businesses understand equipment performance trends and pinpoint issues affecting availability. Regular analysis of these metrics allows companies to make data-driven decisions to enhance maintenance practices and resource allocation. Tracking KPIs also provides insights into the effectiveness of preventive maintenance programs and training initiatives. By consistently evaluating these indicators, businesses can implement strategies to improve equipment availability, optimize operations, and achieve better performance outcomes.
Data Collection and Analysis
Data collection and analysis are foundational to measuring and improving equipment availability. By systematically gathering data on equipment performance, downtime, and maintenance activities, businesses can gain valuable insights into operational efficiency. Employing digital tools and sensors facilitates real-time data capture, enhancing accuracy and timeliness. Analytical software can then process this data to identify patterns and trends, such as frequent failure points planned and unplanned downtime, or maintenance bottlenecks. Understanding these patterns allows companies to make informed decisions about maintenance scheduling, inventory management, and resource allocation. Data analysis can also help predict future equipment failures, enabling proactive measures to prevent downtime. Visualization tools, like dashboards, provide an accessible way to interpret complex data and communicate findings to stakeholders. By leveraging data collection and analysis, businesses can continuously refine their strategies for maintaining high equipment availability, ultimately leading to improved productivity and reduced operational costs.
Continuous Improvement Practices
Continuous improvement practices are essential for sustaining and enhancing equipment availability over time. The philosophy of continuous improvement involves regularly evaluating processes and making incremental changes to boost efficiency and performance. Techniques such as Plan-Do-Check-Act (PDCA) cycles and Kaizen encourage iterative enhancements by fostering a culture of ongoing evaluation and feedback. In the context of equipment availability, continuous improvement means consistently analyzing performance data, identifying areas for enhancement, and implementing strategies to keep machine availability measures reduce downtime. Engaging employees at all levels in this process can lead to innovative solutions and empower them to take ownership of maintenance practices. Regularly reviewing maintenance procedures and incorporating technological advancements, such as predictive analytics, can further optimize equipment operations. By committing to continuous improvement, businesses can maintain high equipment availability, adapt to changing operational demands, and ensure long-term success in a competitive environment. This approach not only enhances equipment performance but also supports overall organizational growth and resilience.
Benefits of High Equipment Availability
Cost Savings and Efficiency
High equipment availability translates directly into cost savings and operational efficiency. When equipment is consistently operational, businesses can avoid the high costs associated with emergency repairs and unplanned downtime. This stability increase machine availability allows for more predictable maintenance budgeting and reduces the need for costly rush orders of spare parts. Efficient equipment use also leads to optimized production schedules, ensuring that resources are utilized effectively and waste is minimized. Moreover, reliable equipment availability enhances workforce productivity, as employees can perform their tasks without interruptions, leading to better output and quality. Streamlined operations reduce the need for overtime and other compensatory measures, further decreasing labor costs. In turn, these efficiencies contribute to a more competitive market position, allowing businesses to offer products and services at more attractive price points. By maintaining high equipment availability, companies can achieve significant cost savings, improve operational efficiency, and enhance profitability in the long term.
Enhanced Customer Satisfaction
High equipment availability is a key driver of enhanced customer satisfaction. When equipment functions optimally, businesses can meet production deadlines and deliver products and services on time, maintaining customer trust and loyalty. Consistent availability ensures that companies can fulfill orders without delays, which is particularly important in industries with tight timelines and high customer expectations. Reliable operations improve machine availability also enable businesses to maintain quality standards, as equipment is less likely to produce defects when well-maintained and operational. This reliability directly translates to customer confidence in the product or service being offered. Furthermore, businesses that consistently meet or exceed customer expectations can leverage this reputation to gain a competitive advantage, foster long-term relationships, and encourage repeat business. By prioritizing high equipment availability, companies not only improve operational performance but also strengthen their brand reputation, leading to increased customer satisfaction and sustained business growth.
Competitive Advantage in the Market
High equipment availability confers a significant competitive advantage in the market. Companies that maintain reliable operations can offer superior service levels, ensuring timely delivery and consistent product quality. This reliability can differentiate a business from its competitors, attracting customers who value dependable service. Additionally, high equipment availability allows companies to be more agile, responding quickly to market demands and customer needs. This flexibility can be crucial in capturing market share and entering new markets. Furthermore, operational efficiency gained from high equipment availability often translates to cost savings, enabling businesses to offer more competitive pricing or reinvest in innovation and improvement. A reputation for reliability and quality can also enhance brand image, making a top asset availability company the preferred choice in its industry. Ultimately, by prioritizing equipment availability, businesses not only enhance their operational efficiency but also strengthen their market position, driving growth and success in a competitive landscape.
Using an inventory management tool, like the one in Rentman, can help support your work by automating much of the process. Discover how Rentman can become your one-stop platform for all equipment availability, tracking, and scheduling.
FAQ
Frequently asked questions
No items found.
Previous blog posts
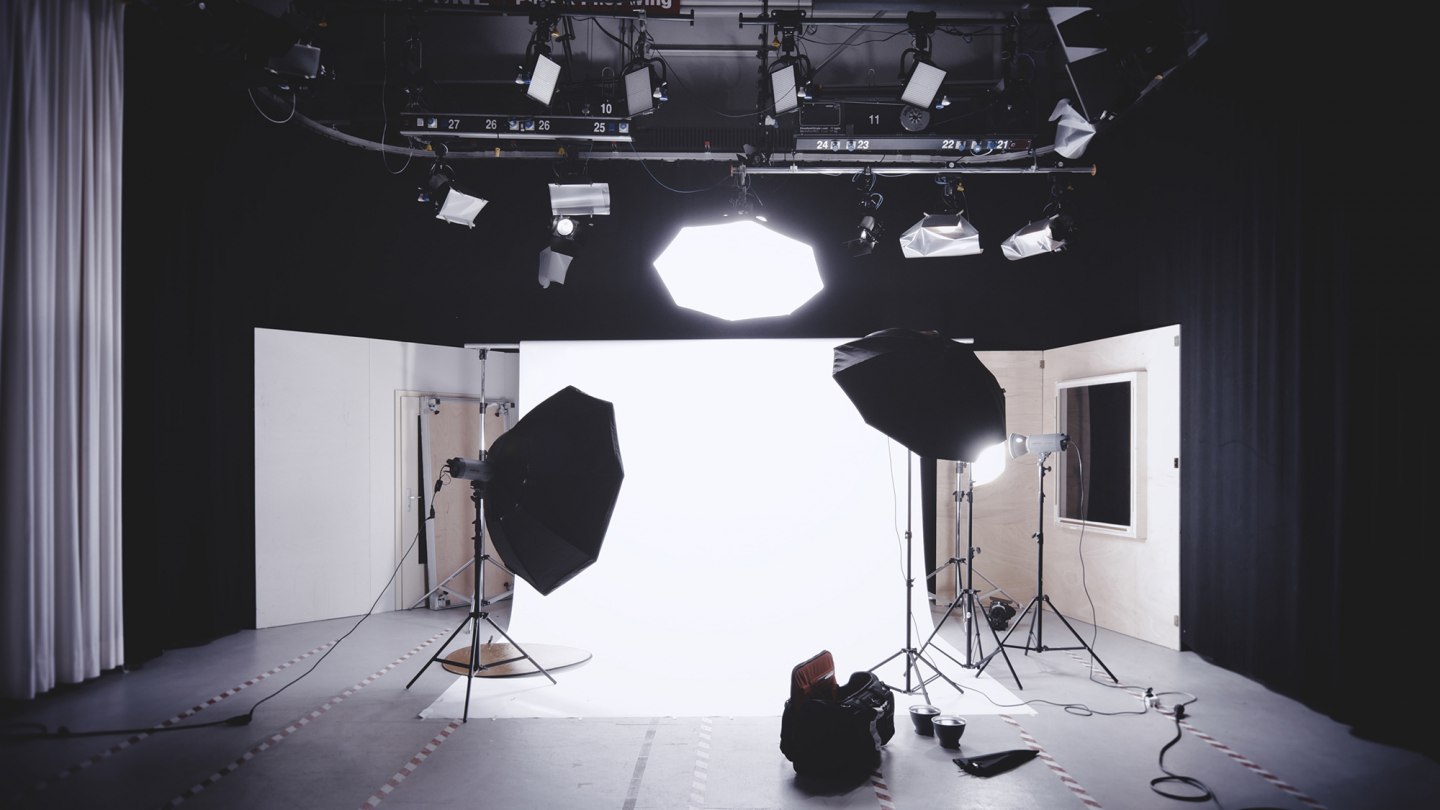
Creating Winning Client Quotes to Secure Jobs in AV, Events, and Media Production
Creating Winning Client Quotes to Secure Jobs in AV, Events, and Media Production
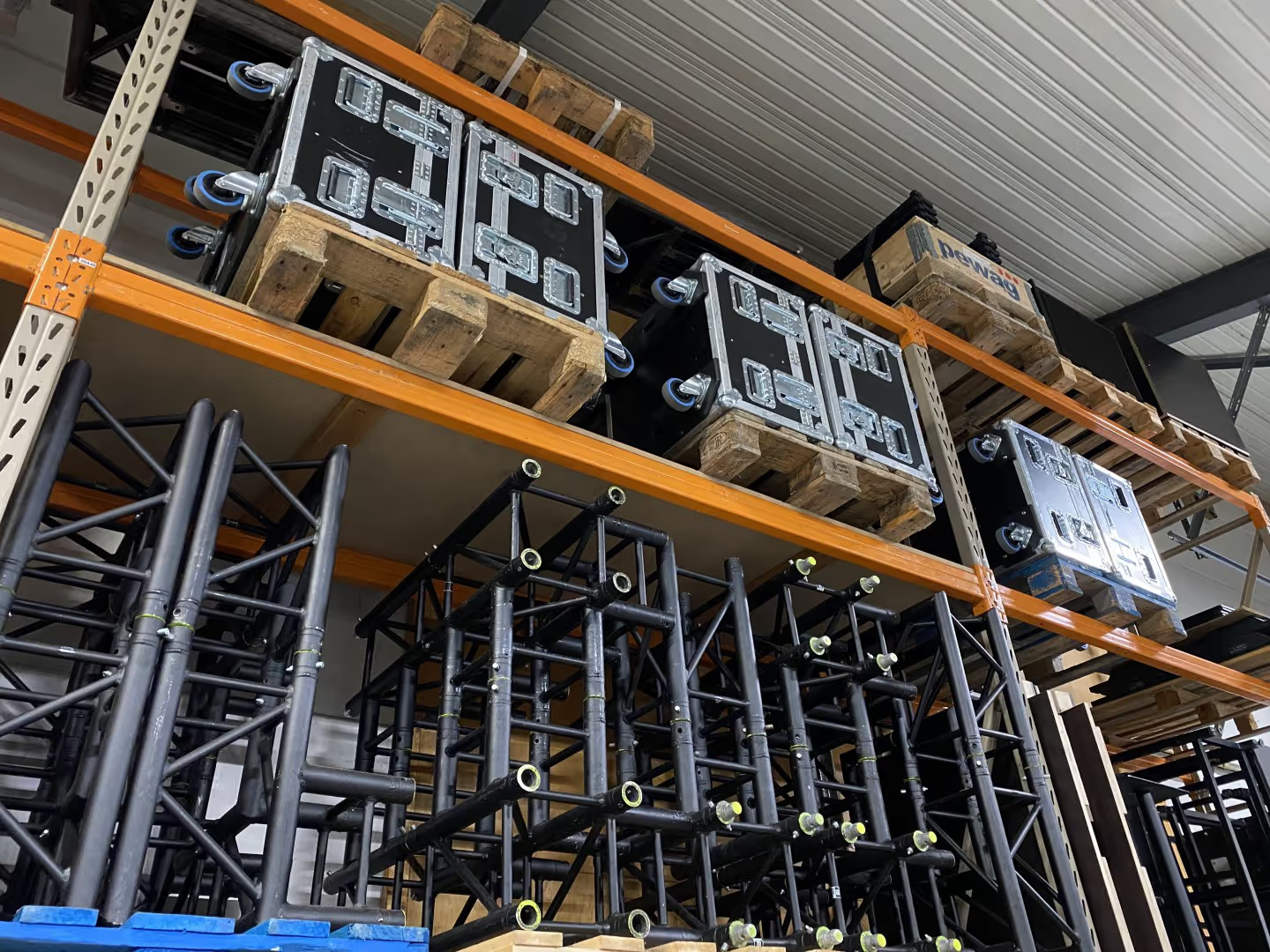
Unlocking Efficiency: How Warehouse Management Software Transforms Operations in AV, Events, and Media Production Industries
Unlocking Efficiency: How Warehouse Management Software Transforms Operations in AV, Events, and Media Production Industries
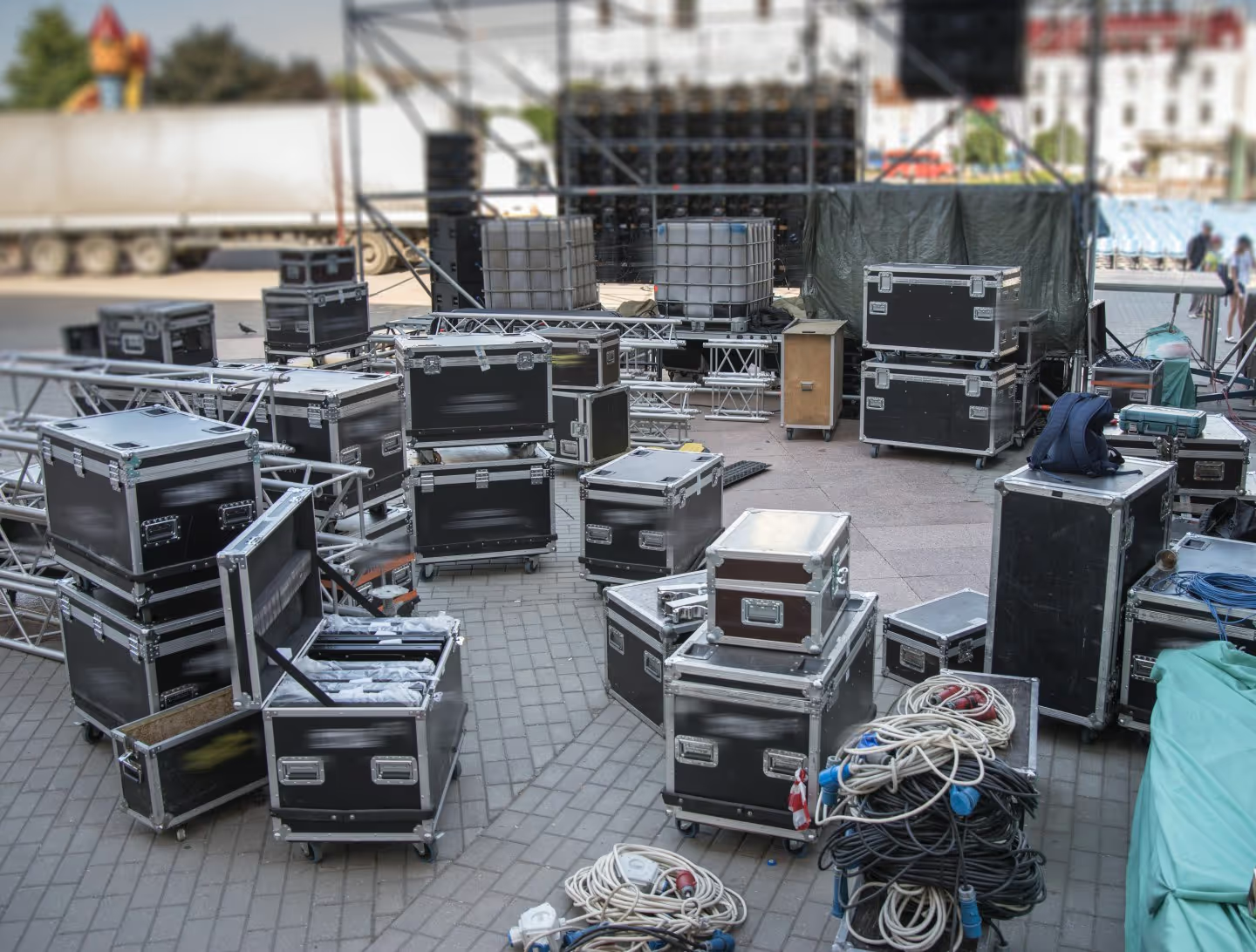