Understanding Asset Tags for Equipment: A Comprehensive Guide for Event Businesses
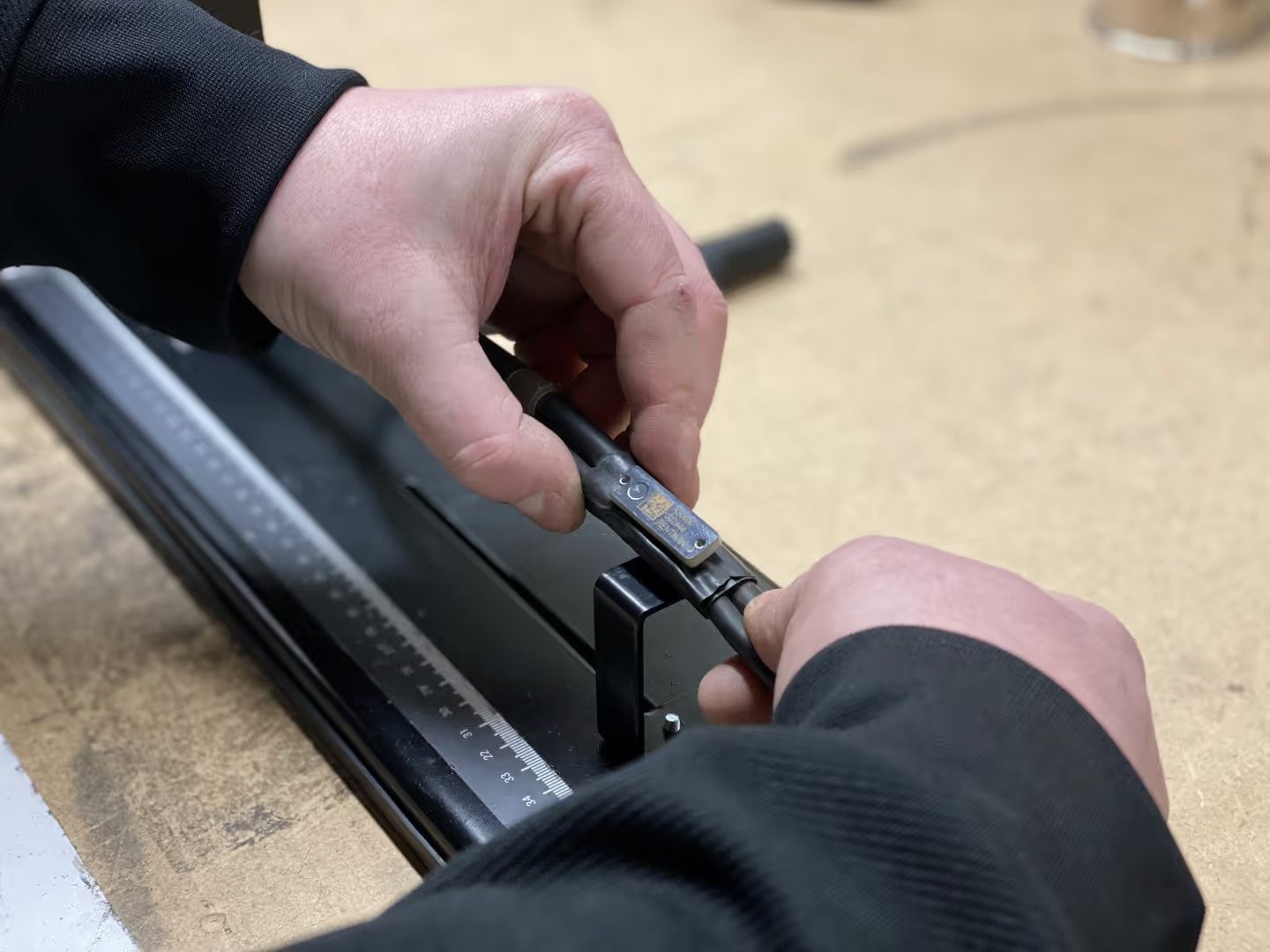
In the bustling world of event production, keeping track of equipment is crucial for maintaining efficiency and accountability. Event companies rely heavily on specialized gear, from audiovisual setups to staging equipment, making asset tags indispensable tools in this endeavor.
These tags, often bearing unique identification numbers or barcodes, allow businesses to monitor the location, status, and maintenance records of their valuable assets. Understanding how asset tags function and their benefits can empower event production teams to streamline operations and reduce the risk of loss or mismanagement.
In this guide, we will delve into the various aspects of asset tags for equipment, providing insights that are relevant to event businesses of all sizes.
1. Introduction to Asset Tags
2. Benefits of Asset Tags for Equipment
3. How to Implement Asset Tags
Introduction to Asset Tags
Importance of Asset Tags
Asset tags and asset labels for equipment play a vital role in the smooth functioning of any event production company. They are essential for tracking the whereabouts of event-specific gear, such as lighting rigs, sound systems, and staging components. By ensuring each piece of equipment is tagged, event teams can maintain an up-to-date inventory without much hassle. Asset tags help prevent theft and loss by making it easier to identify missing items, which is especially important for on-location events.
Additionally, they provide a systematic way to record the maintenance history and condition of each asset, which is crucial for ensuring gear longevity, safety, and performance during events. They also enable quicker audits and compliance checks, saving time and resources, especially during event setups and teardowns. In essence, asset tags and labels offer a straightforward solution for managing event gear efficiently, reducing human error, and supporting informed decision-making. Their importance cannot be overstated as they contribute significantly to operational efficiency, equipment management, and event cost control.
Types of Asset Tags
Asset tags for equipment come in various types, each catering to different event production needs. The most common types include barcode tags, RFID tags, and QR code tags. In event production, barcode tags are widely used due to their simplicity and low cost. They can be printed and scanned easily to track gear such as cameras, microphones, and staging elements, but require a direct line of sight for print and scanning. RFID tags, on the other hand, use radio waves to communicate information and can be read from a distance without needing a direct line of sight.
This makes them ideal for environments where quick and efficient asset tracking is required, such as backstage areas or large event venues. QR code tags are similar to barcodes but can store more information and can be scanned using smartphones, adding a layer of convenience for on-the-go production teams. In addition to these, there are tamper-evident tags which show clear signs if they have been removed or altered, offering extra security for high-value or frequently rented equipment. Each type serves a unique purpose, and choosing the right one depends on specific event production requirements.
Benefits of Asset Tags for Equipment
Enhancing Equipment Tracking
Asset tags for equipment significantly enhance the tracking of assets within an event production company. By providing each piece of equipment with a unique identifier, event professionals can effortlessly monitor the movement and location of their assets, which is critical when gear is frequently transported between event venues, warehouses, or rented out to clients. This capability is particularly beneficial in large-scale productions or events where equipment is constantly moved between departments, locations, or even countries. The real-time tracking enabled by asset tags helps reduce misplacement and loss, ensuring that essential equipment like lighting, sound systems, and stage components is always available when needed.
Moreover, it facilitates the quick retrieval of assets, saving valuable time and effort during time-sensitive event setups or breakdowns. Enhanced tracking also allows for better maintenance scheduling, as event companies can easily check which equipment is due for service, preventing unexpected downtime during critical events.
Additionally, it aids in compiling accurate inventory reports, which are essential for financial audits, compliance, and insurance purposes. Overall, asset tags provide a reliable method to keep track of event gear, boosting operational efficiency and reducing the likelihood of equipment-related disruptions, which can be costly for live productions.
Improving Inventory Management
Asset tags and stickers for equipment play a crucial role in enhancing inventory management for event production teams. By tagging each asset, event planners and technicians can maintain a precise and up-to-date inventory record of technical equipment, staging materials, and decorative elements.
This accuracy is vital for making informed purchasing decisions and avoiding unnecessary expenditure on surplus or redundant equipment. Asset tags simplify the process of conducting inventory audits by allowing for quick and efficient scanning of high-volume event gear, which reduces the time and labour traditionally required, especially for large-scale productions or events with multiple locations. This efficiency is especially important for event production companies with a vast number of assets spread across various storage facilities, warehouses, or on-site venues.
Additionally, asset tags help maintain consistency in inventory data, minimising human errors that can occur with manual record-keeping, which is crucial during busy production schedules. They also enable automated alerts for maintenance or replacement needs, ensuring that equipment such as sound systems, LED screens, and rigging is always in optimal condition. By improving the overall management of inventory, asset labels and tags contribute to cost savings, better resource allocation, and more streamlined operations, ultimately enhancing the profitability and smooth execution of events.
How to Implement Asset Tags
Choosing the Right Tags
Selecting the appropriate asset tags for equipment is a critical step in the implementation process, especially in the event production industry, where the variety of equipment and environments can be vast. The choice depends on several factors, including the type of equipment, the environment in which it operates, and the specific tracking requirements of the event company. For instance, barcode tags are cost-effective and suitable for indoor settings where direct scanning is feasible, such as in production studios or during indoor events.
However, for assets located in outdoor venues or challenging environments, or for equipment requiring long-range tracking, RFID tags may be more appropriate due to their durability and capability to be read from a distance—ideal for large festival grounds or complex event setups. QR code tags offer flexibility and additional information storage, making them a good fit for assets that require detailed data access, such as audio-visual gear, lighting systems, or rental items. It's also essential to consider the material of the tags, ensuring they are durable and can withstand environmental conditions such as heat, moisture, or even rough handling during transport to various event sites.
By carefully evaluating these factors, event production companies can choose the right asset tags that align with their operational and business needs, maximising the efficiency of their event equipment management strategy.
Best Practices for Tagging Equipment
Implementing asset tags for equipment effectively requires adherence to best practices to ensure optimal functionality and efficiency, especially in event production where time and equipment handling are critical. First, it is important to tag equipment in a consistent location across all assets, making it easy to locate, label, and scan during event setup or tear down. This consistency aids in quick identification and reduces scanning errors, particularly when event crew members are working under tight deadlines.
Tagging should occur at a time when it will cause minimal disruption to operations, such as during scheduled maintenance, post-event equipment checks, or inventory audits. Additionally, ensure the metal asset tags are securely attached to prevent them from being accidentally removed or damaged during transport, installation, or use in demanding environments like outdoor events. It's also beneficial to regularly review and update the tagging system to accommodate any changes in inventory or technology, ensuring it remains efficient as new equipment is added or old items are retired. Training staff on how to correctly use and manage asset tags is crucial for maintaining the system's integrity, especially for event production teams that work in multiple locations or with various crews.
Lastly, integrate the asset tagging system with existing event management and rental software to streamline processes and enhance data accuracy. By following these best practices, event production companies can maximise the benefits of their asset tagging system, ensuring smooth operations and safeguarding their valuable equipment.
FAQ
Frequently asked questions
No items found.
Previous blog posts
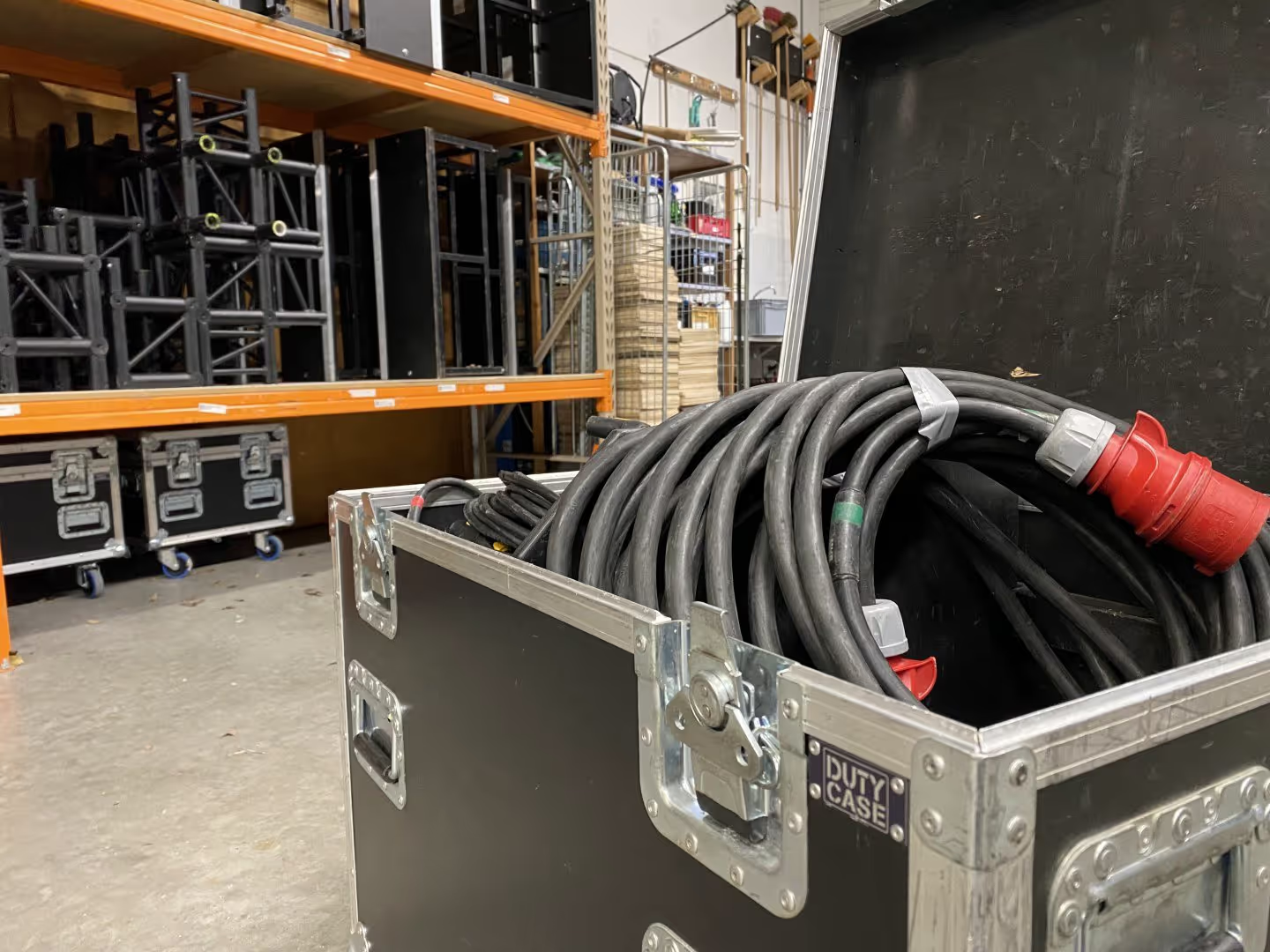
The Essential Guide to Choosing the Right Labelling Equipment for Your Event Rental Business
The Essential Guide to Choosing the Right Labelling Equipment for Your Event Rental Business
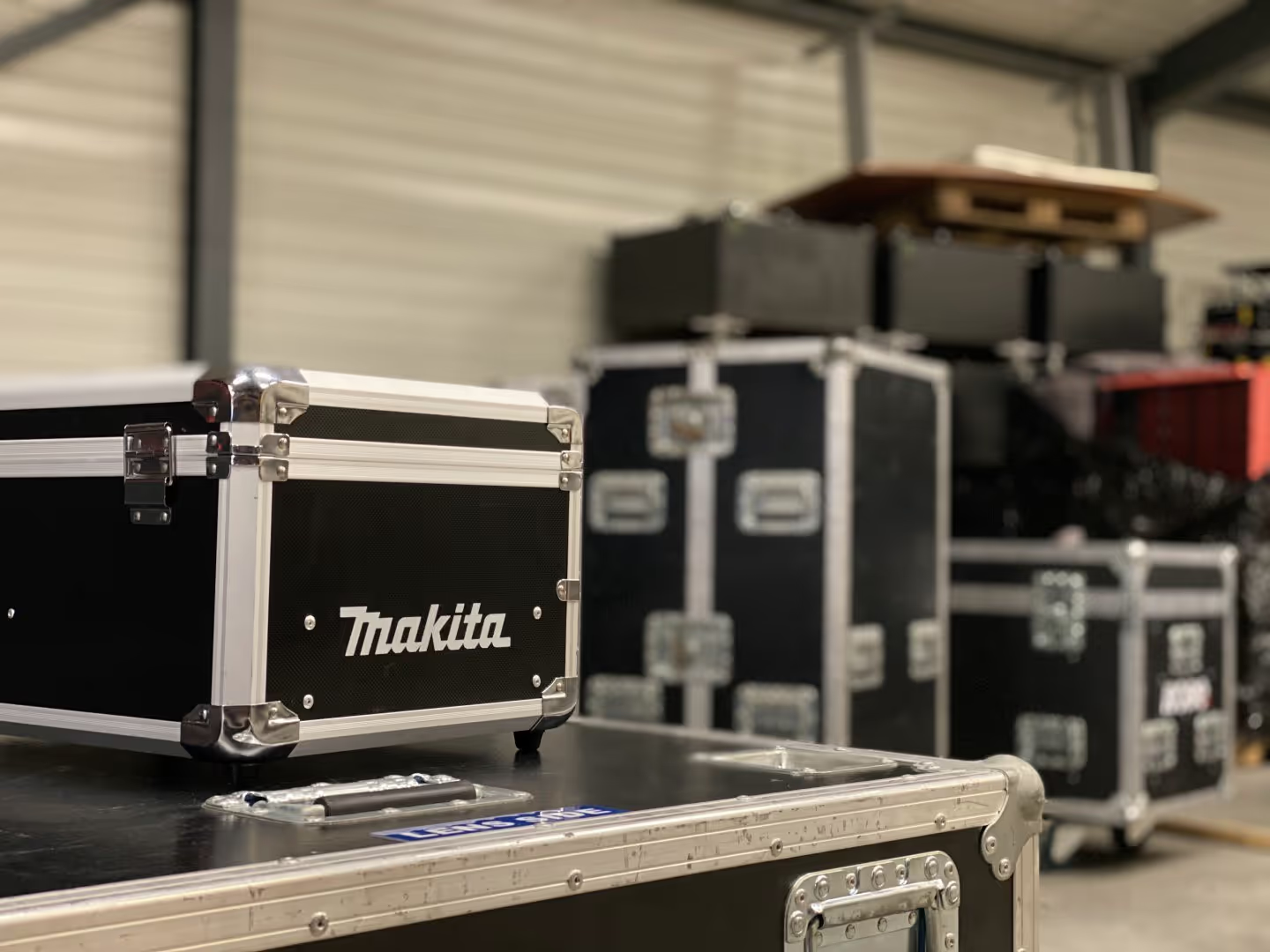
The Ultimate Guide to Equipment Coverage in the Event Industry: What You Need to Know
The Ultimate Guide to Equipment Coverage in the Event Industry: What You Need to Know
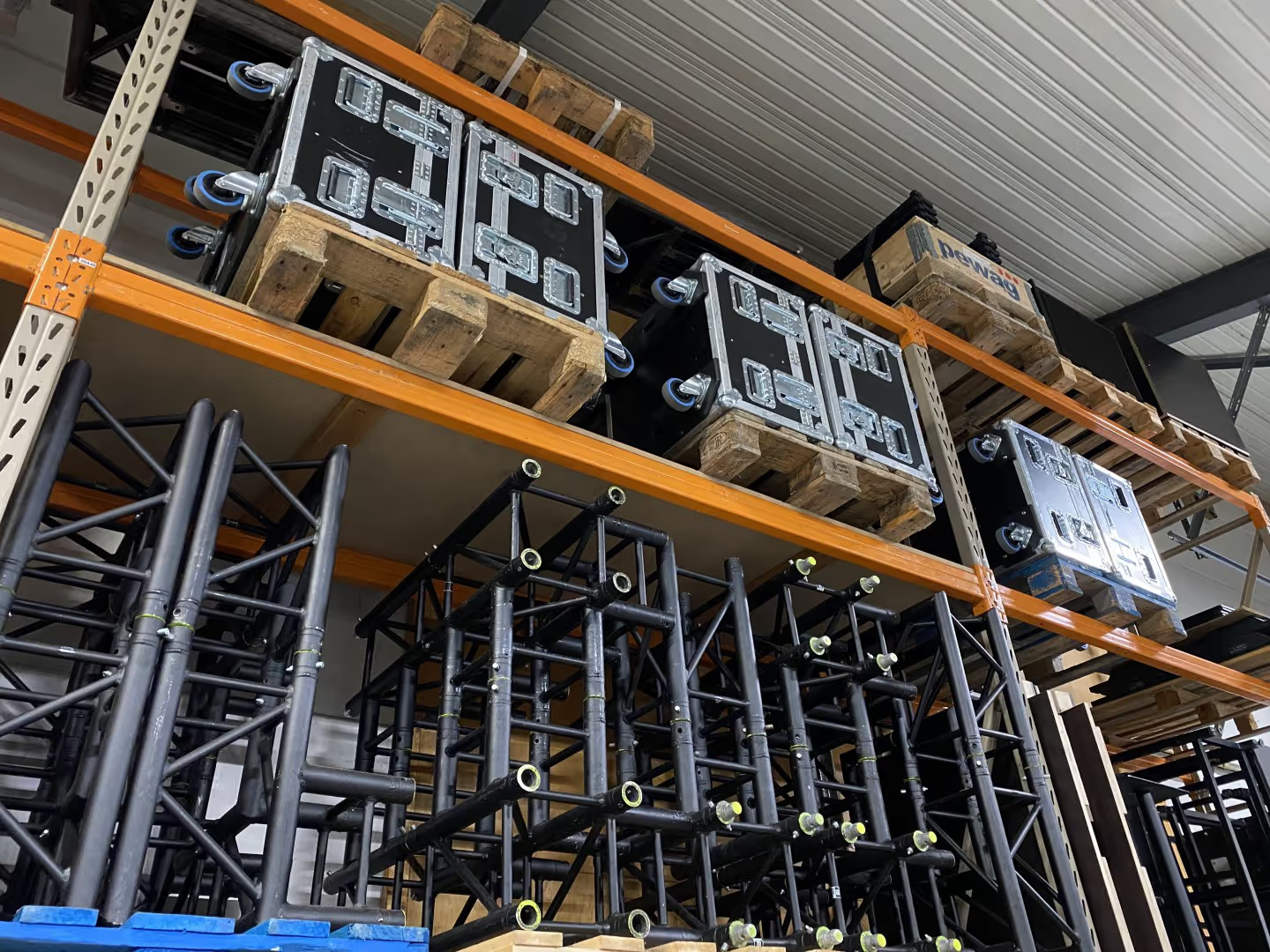